1
自動車向け塗装外観検査の現状と課題
近年、特に欧米各諸国のインフレに伴う検査員コストの上昇に加え、雇用市場の流動性が高い事が原因の一つとなる不安定品質、高度な専門知識と熟練経験の必要性、技術継承、さらに日本国内では少子化による検査員不足など、自動車向け外観検査において様々な課題を抱えている。
目視検査には一定の熟練度が要求され、専門の検査作業員による作業が行われている。目視検査に要求される欠陥検出レベルも年々厳しくなり、特に日本国内では直径0.3 mm程度の非常に小さな欠陥も検査のターゲットになってきている(Fig. 1 赤丸部)。一方で、人による作業であるため、OK/NG判定が検査作業員により異なることや見逃しによる欠陥流出などのリスクもある。長時間の目視作業による疲労からくる検査品質のばらつきも人起因の課題である1)。
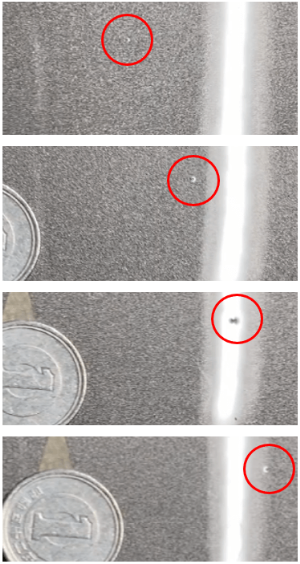
Fig. 1 An example of how defect looks.
また、様々な業界・分野でデジタルデータの活用やDX化が進んでいる中で、外観検査においてはアナログ作業・紙による管理部分も多く、検査情報が製品品質の源流改善や不具合の真因解決に十分活かされていない状況にある。
2
Eines Vision Systems社について
2.1 会社概要
1992年創立のEines Vision Systems社(以下、Eines社)は、スペインに本社を構えるコニカミノルタのグループ会社である(https://www.eines.com)。自動車生産の品質検査自動化システムに力を入れており、欧州ファクトリー・オートメーションへの知見とアジャイルな開発体制で、グローバルで複数の自動車会社への導入実績がある。
2.2 主な製品概要
Eines社は4つの分野でソリューションを展開している(Fig. 2)。
① Quality Inspection:塗装欠陥検査、シーラー検査、シャフト部分の傷、油漏れ検査、異物混入、塗膜粒子検査。
② Metrology:すき間・段差計測(最終組立用システム)、鋳造部品測定、鍛造部品測定。
③ 3-D robot guidance:部品のピッキング、部品挿入、自動シール、組立システム。
④ Part ID and Multi error proofing:ポカヨケシステム、ボディID認識、DOTコードリーダー等。
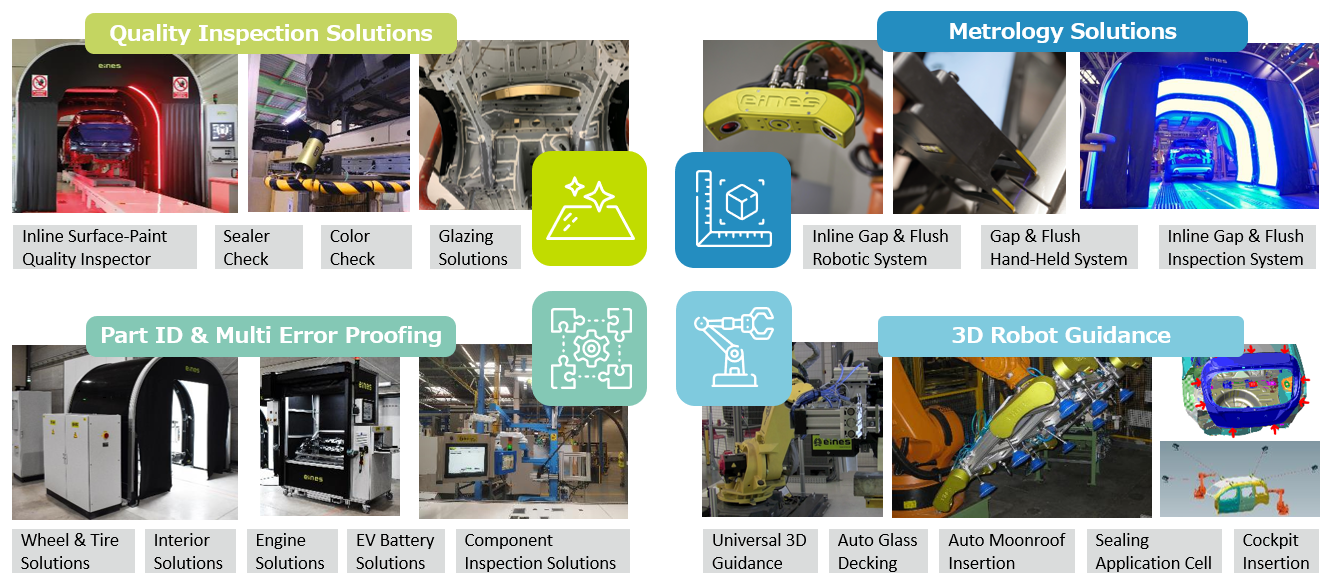
Fig. 2 Eines solutions in 4 groups.
3
自動車塗装欠陥検査システム(esφi)
自動車塗装欠陥検査システムesφi(エスフィー)は、Eines Surface Paint Quality Inspectorの頭文字に由来し、φはpとqの2つのアルファベットを同時に表現している。自動車外装の塗装中に異物混入等により表面に生じた塗装欠陥の目視検査を自動化するシステムであり、以下その特長および技術について詳細に説明する。
3.1 特長
esφiは、トンネル形の欠陥検査システムであり、以下の特長がある(Fig. 3)。
① トンネル形のLED照明と固定カメラにより駆動部が無いため、柵や囲いを設けるなどの安全対策が不要。
② 検査装置自体が軽量・省スペースであり、設置場所の選定がフレキシブル。
③ 高速処理・検査により、高速タクトラインへの導入が可能。
④ 電着塗装(Electric deposition, ED)、下塗り(Primer)、上塗り(Top coat)など、主な塗装検査工程に適応。
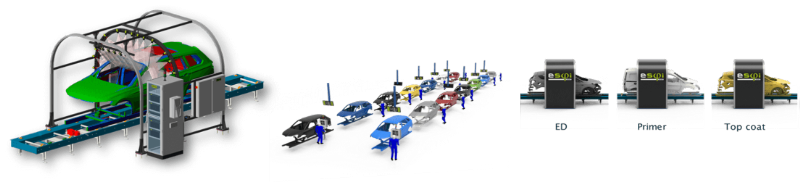
Fig. 3 Features of esφi.
3.2 システム構成
esφiは、トンネル部のメインスキャナー、PCを収納するITキャビネット、制御ボックス、フィニッシュライン用の表示モニター、フィニッシュライン上でオペレータへ検査結果を示すデバイスで構成され、システム全体でも非常にシンプルな構成となっている(Fig. 4)。
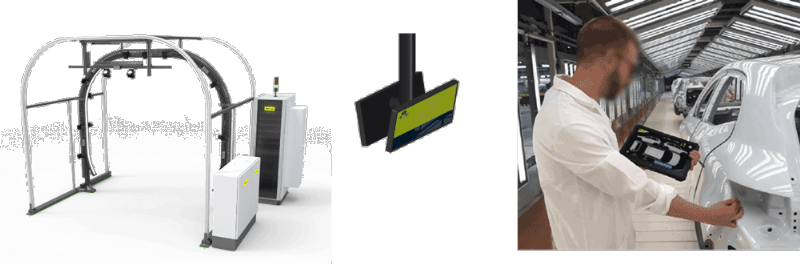
Fig. 4 esφi system configuration.
3.3 技術と強み
3.3.1 基本原理
基本原理としては目視検査で用いられている方法と同等であり、アーチ状に配置されたLED光源からの光が被検査車体の表面で反射している状態をカメラで高速にスキャンする。”光のてこ”の原理(反射面の角度がθ変化すると、反射光の角度は2θ変化する)を利用して欠陥を画像で捉えるため、検査面の微小な傾きを画像の変化で検知することができる。照明と車体との距離が遠いほど、てこの原理が効き、欠陥を明確に捉えることができる(Fig. 5)。
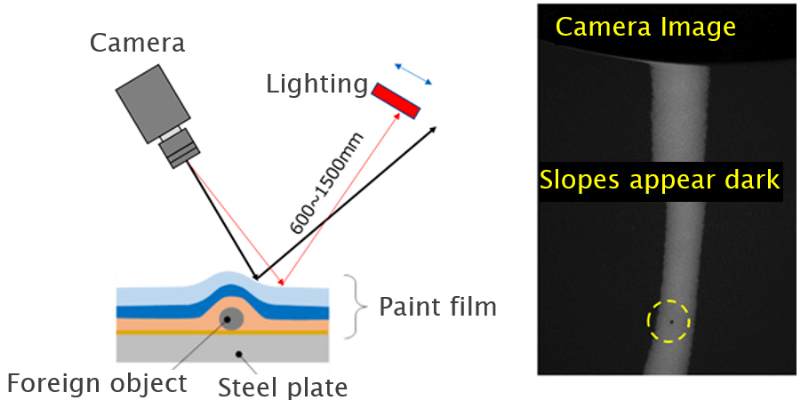
Fig. 5 Painted surface structure and detection principle.
周辺の平らな部分には照明の反射像が映るが、傾きがある欠陥部分では照明外側の暗い領域の反射像が映ることで暗い点となって欠陥を認識できる。また、欠陥部分の写り方は撮影の進行に従って変化する(Fig. 6)2)。
撮影された大量の画像データはPCを使用して専用に開発した高速処理ソフトウェアで処理され、独自のアルゴリズムによって欠陥を検出・分類する。
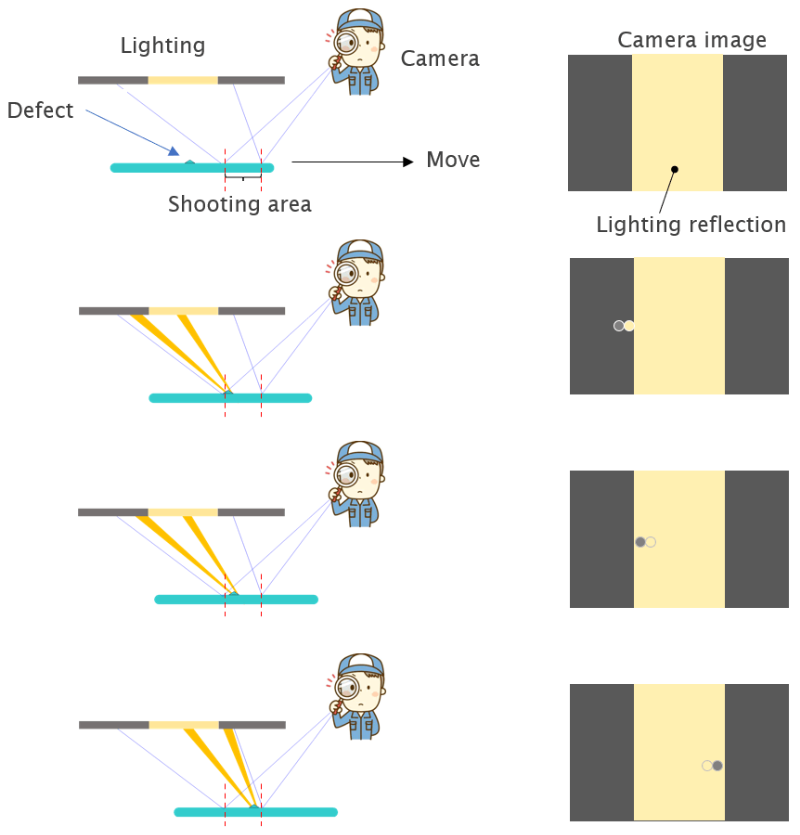
Fig. 6 Images when defects are visible near the light/dark boundary.
3.3.2 欠陥検出能力
対象となる車種/モデル、塗装色、部位等に応じて個別に欠陥を検出・分類することができる。欠陥種類は、ブツ、凹み、スクラッチ、繊維など顧客仕様に応じて分類を行うことができ、AIを利用することも出来る(Fig. 7)。また、同一部品内の欠陥位置の発生ゾーン分けや、欠陥サイズ/形状による判別も可能である3)。

Fig. 7 Defects detected and classified.
3.3.3 シミュレーション技術
esφi導入に際しては対象車種に応じた様々な設計・調整が必要であり、検査装置立上げまでのリードタイムの長さが課題になっていた。Eines社がコニカミノルタのグループ企業となったことで、コニカミノルタの光学・シミュレーション技術を活用した各種ツールを開発・導入し、リードタイム短縮や機能向上に大きく寄与している。その一部技術について紹介する。
① カメラ位置評価ツール
同一のラインで複数車種の検査を行うケースがあるため、全ての対象車種に対応できるよう、カメラのスペックを元に撮影に必要な台数、位置などの評価を行うツールを開発した。基本原理で述べたように、検査の実効領域は車体面に写ったLED光源帯の虚像(以下、明帯)であるため、本ツールでは、顧客より提供された被検査車種の3Dデータを用いてカメラ側から光線の逆追跡を行い、主光線(開口絞りの中心を通る光線)が車体表面で正反射した先にLED光源があるかをトレースすることで、被検査車種の3Dデータ上に明帯がどのように撮影されるかをシミュレーションすることができる。全車種をカバーする視野で、適切なオーバーラップで検査の抜け漏れ無く撮影ができるかなど、実車を用いること無く事前にシミュレーションで確認することができるため、検査装置規模の高精度な見積やキャリブレーション作業の短縮にも繋がっている(Fig. 8, 9)。
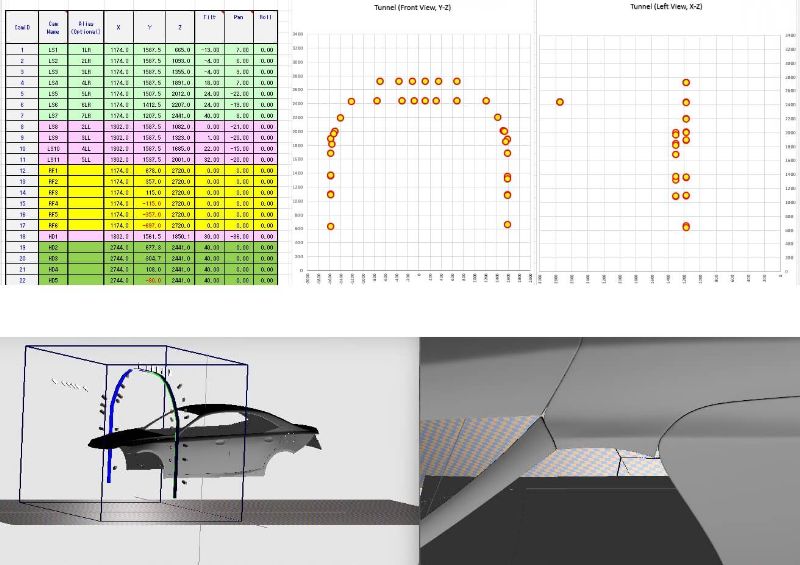
Fig. 8 Camera position evaluation tool.
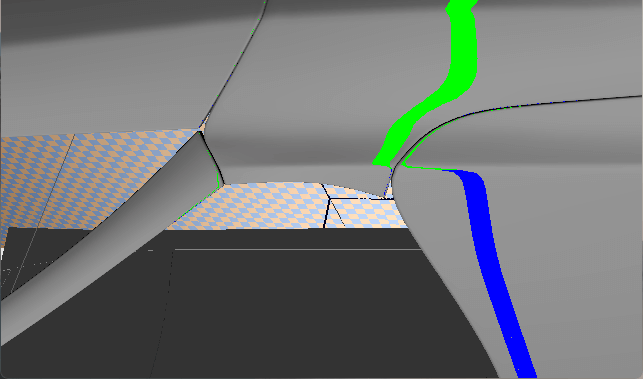
Fig. 9 Bright band confirmation by simulation.
② 擬似欠陥によるAI学習データ拡張
AIを利用した欠陥の分類には、欠陥を学習するための大量の画像データが必要となるが、通常、新規生産ラインにおいては、検出対象となる欠陥がすぐに集まることは稀である。そのため、AI学習のための欠陥を擬似的に作成する技術を開発した。実際の欠陥などの情報を元に欠陥形状は数式化されており、3~4つのパラメーター調整で自動的に多数の欠陥のバリエーションを作り出す事ができる(Fig. 10)4)。
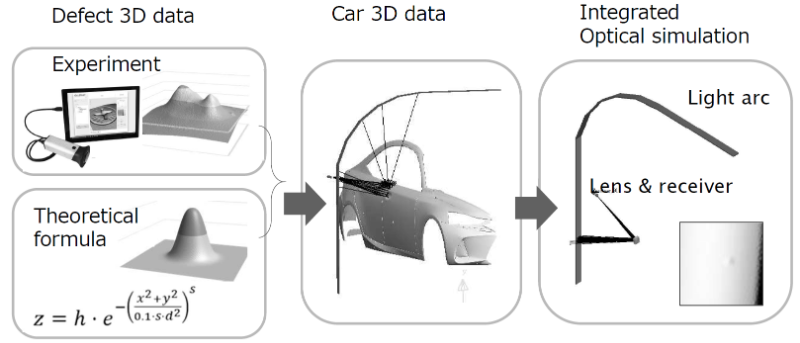
Fig. 10 Data augmentation for deep learning with pseudo defects.
3.4 検査結果と活用
3. 4. 1 検査結果表示
Fig. 11は、フィニッシュラインでの欠陥検査結果の表示例であり、お客様のニーズに応じたフレキシブルな表示ユーザーインタフェースとなっている。塗装欠陥の場所や種類が瞬時に且つ直感的に判るような伝達方法が求められるため、作業者が担当部位の欠陥位置を確認するために図のようにドットで表されており、スマホやタブレットなどの表示デバイスを活用することで、作業員の負担を低減させることにも繋がっている。
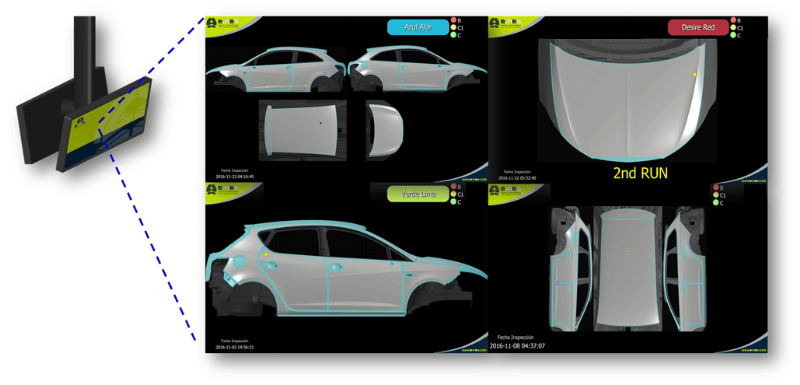
Fig. 11 Example of displaying defect inspection results at the finish line.
3.4.2 検査結果の活用
塗装欠陥種類の詳細分類と分析で源流工程への高品質なフィードバックが可能となり、品質データや品質クレームなどのトレーサビリティを確保することにより、品質管理プロセスの改善に繋げることができる。また、検査・分類結果をオートリペアシステムなどの後工程に連動させることで、生産性向上にも結びつけることができる。
3.5 競合と実績
3.5.1 競合
自動車塗装外観検査には様々な競合手法があり、主にロボットタイプとEines社と同様のトンネルタイプに大別される。それぞれ特徴があるため、検査員による目視検査と合わせて、次の表にまとめた(Table 1)5)。
Table 1 Comparison of inspection methods.
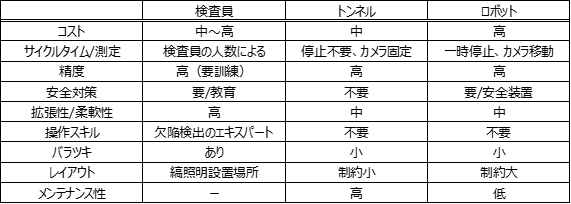
3.5.2 導入実績
esφiはグローバルで導入実績があり、50以上のトンネル形ビジョンシステムの実績がある。
4
まとめと今後
今まで検査員による目視検査を行っていた自動車塗装外観検査を自動化することにより、人手不足の解消、品質の安定化、源流工程へのフィードバックなどの課題解決に貢献することができる。Eines社の商材にコニカミノルタの技術を導入し、品質・導入に関するシナジー効果を生み出している。今後は更にAIの導入などを進める一方で、導入プロセスの効率化などにより、複数年にわたるリードタイムの短縮や少人数での導入を目指していく。