1 はじめに
コニカミノルタでは,これまで産業用インクジェットヘッドの開発を行ってきたが,用途の多様化により少量多品種化が加速するとともに高精度,高生産性,高安定性の要求が年々高まっており,それに伴う品質保証と顧客対応プロセスも複雑化している。一方で昨今,データを活用する技術の進歩,また用途の拡大が目覚ましく,インクジェットヘッド事業においてもデータ活用,データ分析による効率化や品質改善を推進してきた。その中で品質保証のデジタルトランスフォーメーション(DX)を「Digital-QA(Quality Assurance)」として立ち上げ,データを活用したワークフロー変革や市場トラブルの未然防止に取り組んでいる。
2 Digital-QAの目指す姿
2. 1 課題認識
コニカミノルタでは,Fig. 1 のように市場で不具合が発生したインクジェットヘッド(以下IJヘッド)を解析,原因特定を行い,顧客に対する補償と対策内容を決定するプロセスであるRMA(Return Merchandise Authorization)を採用している(Fig. 1)。
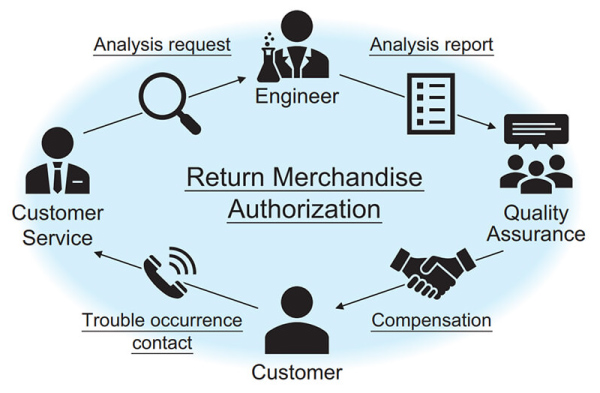
Fig. 1 RMA (Return Merchandise Authorization). RMA is system in series of process for market troubles for IJ head to analyze to identify the cause, compensate and correct in production.
そのようなプロセスにより市場トラブルを素早く察知し,設計起因,生産起因,ユーザー使用環境起因に発生要因を分類することで,製品の品質及び製品のユーザビリティを高めることが出来る。また,製品不具合に対する補償はコストに反映されるため適切に監視,改善していくことが求められる。
しかし,製品の多品種化と顧客要望の高度化に伴って以下のような問題が顕在化してきた。
(1)複数部門での情報のやりとりに時間がかかり,顧客対応リードタイムが長期化する。
(2)情報が分散することで集計,傾向把握が困難なため同様のトラブルが頻発する。
2. 2 活動目的
上記の課題認識を受けて,ここにデジタル技術を導入し,様々な顧客別データを出荷や生産履歴と紐づけて監視,解析を行うためのプラットフォームを新たに構築した。さらにこのプラットフォームを用いて,ワークフローの変革とトラブルの未然防止につなげることにより,顧客対応と品質保証体制をさらに強化することにした。
この一連の活動を品質保証のDXとして「Digital-QA」と命名し,1. 情報の一元管理,2. 品質のリアルタイム監視,3. データによる先んじた品質改善を目指す姿としている(Fig. 2)。
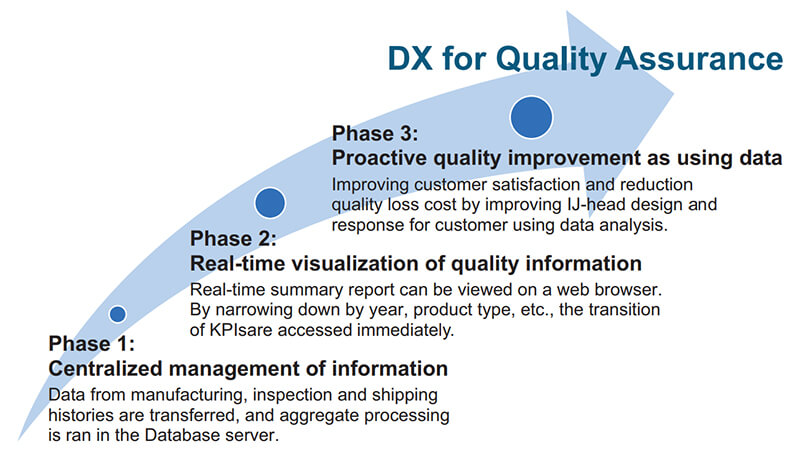
Fig. 2 Roadmap of Digital-QA as digital transformation for quality assurance.
活動は以下の4つのステップに分けて取り組んでおり,次章で詳細について説明する。
① 既存情報のデジタル化と関連付け
② 情報のリアルタイム見える化
③ 顧客対応ワークフローの見直し
④ 傾向分析によるトラブルの未然防止
3 Digital-QA推進の取り組み
3. 1 既存情報のデジタル化と関連付け
顧客対応業務には,不具合情報,解析データ,対応履歴等の様々な情報が存在し,従来はExcel,メール,紙など様々な媒体で共有されていた。これらは一括で検索することが出来ないことに加えて型式,用語等が異なるため集計することが困難である。
そこで市場不具合情報,顧客対応履歴,生産/出荷情報を一元管理できるプラットフォームを構築した。システムの全体概要をFig. 3 に示す。
市場不具合情報は顧客から不具合現象をヒアリングした内容を電子帳票に入力する。この電子帳票は製品品種によって入力フォームが分かれているが,集計分析を容易にするため共通部分は型式,用語が統一された構成としている。電子帳票に入力された情報は構造化データとしてデータベースに蓄積される。顧客対応履歴は品質保証部門,営業部門が共通の電子帳票に入力する。生産/出荷情報は他管理システム及び測定装置等から必要な情報がリアルタイムにデータベースに追加され,電子帳票から入力されたデータと関連付けを行っている。
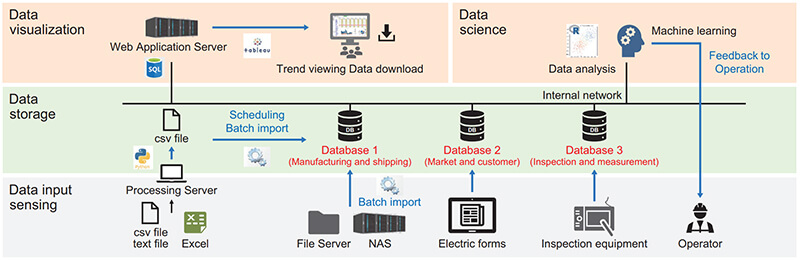
Fig. 3 Conceptual diagram of Digital-QA platform. The traceability is greatly improved by establishment a data infrastructure that accumulates the information regarding production, shipment and market data. In order to analyze such data, BI and machine learning can be used with the internal network.
これら一連の情報のデジタル化により,生産から出荷,市場での使用状況,製品不具合/補償履歴の全てがシリアルに紐づくプラットフォームとして製品のトレーサビリティを確立している。さらにこのプラットフォームを活用することにより,製品品種ごとの集計や,トレンド解析を容易に行うことが出来る。
3. 2 情報のリアルタイム見える化
前述のプラットフォームには日々大量のデータが入力されているが,この中から品質を監視するために重要な指標をFig. 4 の様にWeb画面に一覧表示する品質管理ダッシュボードを作成した。
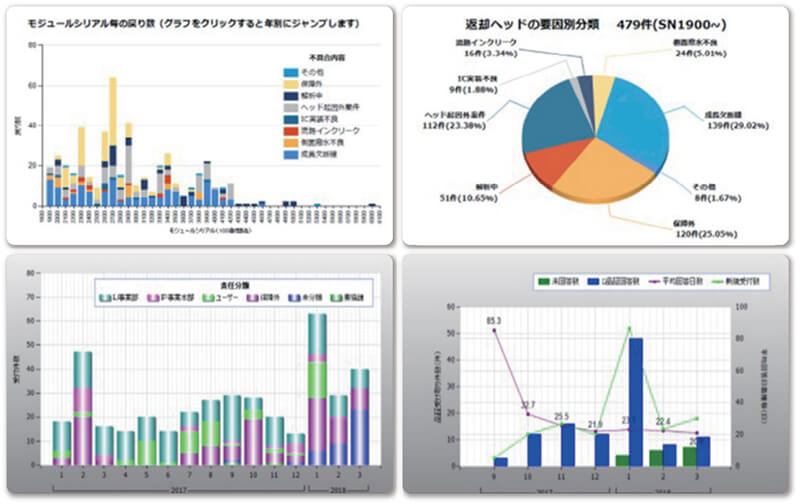
Fig. 4 Real-time automatic aggregation in the quality control dashboard. Summary reports can be viewed on a web browser and the transition of KPIs are accessed immediately by narrowing down by year, product type, etc.
データの見える化を行うツールとしてBI(Business Intelligence)ツールを選定し,部門横断的に管理者を設定し,監視する指標の選択を行っている。品質を測る指標としては製品の歩留まり等が一般的に用いられているが,それに加えて直接測定することが困難な顧客目線での満足度を評価するため,顧客対応の一連のワークフローが完了するまでに要した日数,および長期化案件数を顧客満足度のKPIとして定義している。
Web画面上で表示することで場所に関わらず品質情報にアクセスすることが可能となり,情報はリアルタイムにアップデートされる。品質管理体制の強化とともに,データの集計作業や報告資料作成にかかる時間がほぼ無くなるため,年間数千万円規模の工数削減によるコストメリットも得られている。
3. 3 顧客対応ワークフローの見直し
顧客対応には営業,品証,開発の複数部門が関連してワークフローを形成している。そのため部門間の情報共有がボトルネックになることが度々起こるが,電子帳票と品質管理ダッシュボードを用いることで,必要な情報のみを瞬時に検索しつつ,情報共有をリアルタイムに行うことが可能となった。それにより対面コミュニケーション量が減少し,承認ルートも自動化されるためワークフロー全体が効率化される。
その効果として,前述の顧客満足度KPIとして定義した顧客対応の所要日数はシステム導入を行った3年で1案件あたり40日から15日と半減以下となっている(Table 1)。
Table 1 Comparison of period of response to customers between before and after Digital-QA. After Digital-QA, period for response to customers became less than 1/2.
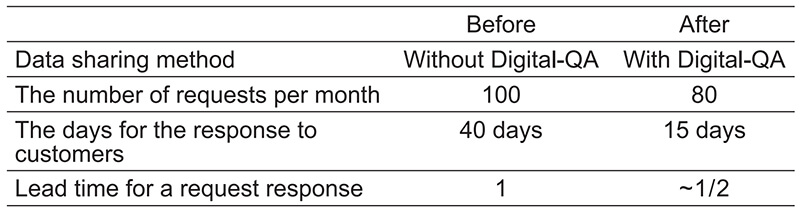
3. 4 傾向分析によるトラブルの未然防止
プラットフォームに蓄積されたデータから傾向分析を行い,市場トラブルが発生したシリアルと類似した環境で使用されている製品,または同一ロットで生産された製品については追加解析,場合によってはトラブル発生前に交換や出荷停止等の処理がなされる。データ分析には品質管理ダッシュボードをドリルダウンして分析する場合もあれば,R等の統計解析ツールを使用する場合もある。
4 データ活用による品質改善
データ分析により製品品質向上に繋がった事例のひとつを紹介する。
電気的異常の原因解析におけるデータ分析活用
IJヘッドの典型的な不良として電気的異常がある。IJヘッド内部のピエゾ素子に電圧を印加することでノズルからインクは射出されるが,この印加される電圧が何かしらの異常により設定された電圧,タイミングからずれると正常にインク射出は行われず,画像異常を引き起こす。電気的異常の原因は多岐にわたるため,特定し根本的な解決を図るのにはかなりの労力を要する。
まずこれまでの知見に基づき,インク加温による筐体の変形または断線が起きたと推定し調査したが,実験では再現されなかった。
そこで,プラットフォームに蓄積されている過去に発生した電気的異常の事例を調査した。過去データには1000件以上の電気的異常の発生状況や解析結果が保管されており,ここから統計的手法により類似点を解析した。結果,不具合発生時期とインク種類の特徴量が有意に相関しており,水系インクを使用している複数の顧客で,冬季に電気的異常が発生しているという特徴が抽出された。
再現実験として冬季の使用停止時における保管環境に合わせて,乾燥を防ぐためにIJヘッドをインク,洗浄液に浸漬させた状態で同様な異常が発生するか実験を行った。結果,Fig. 5 の様に3か月程度で想定通り電気的異常が発生することが確認された。
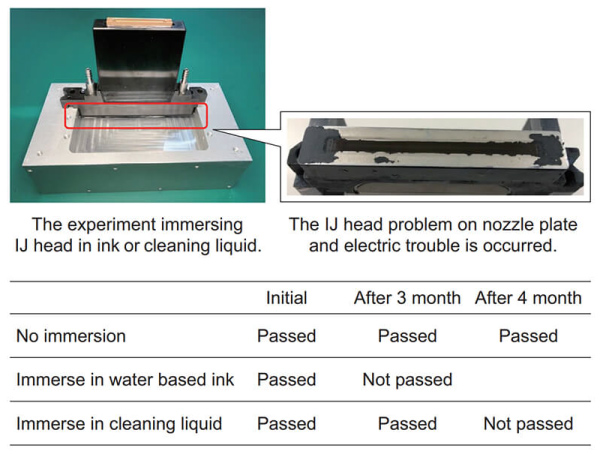
Fig. 5 Experiment as reproduce int the environment of non-operation period, such as night or weekend of IJ head in customer. The electric trouble occurs when the IJ head is immersed in ink or cleaning liquid for a long period.
ノズル板面に異常が見られたことから,顧客の保管環境による外装部材の劣化が根本原因ということが分かり,顧客に対して保管方法の変更を提案することで,その後同様の異常の発生は無くなっている。
このように製品情報,異常現象,顧客使用環境を収集し網羅的に解析,課題解決する一連の流れは従来困難だったことである。本例は下流側である顧客対応による解決であったが,さらに上流側の生産,設計段階での課題解決プロセスにおいても今回と同様なアプローチが有効に働くことが考えられる。
5 まとめ
本稿では,インクジェットヘッドの品質保証プロセスへのデータ活用による顧客対応強化の取り組みの一部を紹介した。我々のビジネス体系に合った独自のカスタマイズを加えたシステム構築により,多くの成果が得られるようになってきている。今後は今回構築したシステムを拡張し未だ現場で眠っているデータを取り込んでいくとともに,様々なアプリケーション(BI,機械学習,画像解析等)を導入していくことで顧客要望を満たす品質の実現につなげていく。