1
はじめに
プロフェッショナルプリント事業の製品は多様化する顧客・市場ニーズにいち早く応えるため、商材の多品種・小ロット化が進んでいる。しかし、部品生産においては金型を用いた大量生産方式での生産が依然として主流となっており、開発・設計のスピード及び量産化リードタイムなどは従来と大きな変化はなく、顧客・市場ニーズへのスピーディーな対応に課題が生じている。また、コスト面においても膨大な金型初期投資が必要となり損益を圧迫することで顧客ニーズに合わせた多様な製品の上市の足かせとなっている。その解決策として近年アディティブマニュファクチャリング (Additive Manufacturing, AM) が着目されている。AMはこれまで製品試作での活用が主流で活用範囲は限定的であったが、近年装置の進化により生産品質・スピードが向上してきており、また装置自体の低価格化が進展していることも追い風となり、コニカミノルタでは量産部品への適用に向けて検討が加速している。
AMに期待する価値は顧客・市場ニーズに応えるためにエンジニアリングチェーン及びサプライチェーンを変革することにある(Fig. 1)。これはコニカミノルタだけでなく今後の製造業全体において将来技術として期待され、様々な業界で検討が進んでいる。1)
➀ AMによるエンジニアリングチェーンの価値:商品価値の最大化を図る目的で、AMの形状自由度の高さを活かした高機能化設計を採用することが可能になる。更に複合一体化設計によって部品点数を削減し、部品費や組立費等の製造原価の削減に繋がる低コスト化を同時に成立させることも可能である。また、設計確認のための試作と量産の工法を共通のものとすることが容易であることから結果的に製品化リードタイムを短縮することが可能であることも利点である。
② AMによるサプライチェーンの価値:金型を要さない生産方法であるため、金型投資費及び維持費、在庫管理費、在庫ロスの削減から利益の最大化を図ることに繋がる。加えて、現地生産や多拠点生産により地政学的変動リスクと環境負荷・物流の最小化を図ることも可能である。
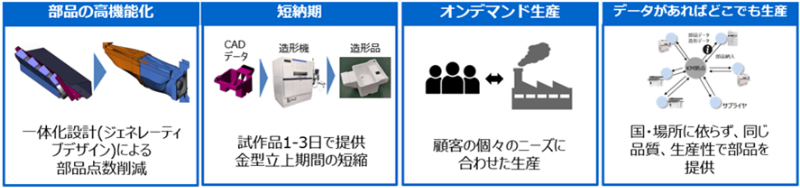
Fig. 1 Strength of Additive Manufacturing
上述した変革の効果は生産規模に依存し大きくなる。しかし生産数の多い部品では成形等の他工法で製造される場合の部品費が安いためAM生産のコスト効果を享受することができない。即ちAM生産対応を行う製品の種数を増しそれぞれの機種でAM生産に切り替えていく部品の比率を高めていくことが重要となる。しかし実際にAM適用を図ることを検討した段階で、品質面では造形精度の向上、コスト面では主に造形材料費が高いことによる製造原価低減が課題であり、AM生産への切り替えが進まない問題があることが分かった。また、設計自由度の高さを活かす設計ノウハウの不足も問題であると言える。そのため、開発部門と生産部門が一体となって新たなAM設計・生産体制を敷き品質・生産性向上技術の開発に取り組み、AM適用事例の蓄積を進めつつ生産規模を高めていくことを目指すこととした。本稿ではAM生産部品適用の拡大を図る上で行ってきた生産面・設計面での技術取組について紹介する。
2
AM技術概要
コニカミノルタでは量産適用においては生産性の高さを備えていることを前提とした上で、AMの強みである設計自由度の高さと材料自由度の高さを備えているものが適していると考えた。最終的にはそれらを満たすパウダーベッドフュージョン (Powder Bed Fusion, PBF) 方式が適切であると判断し選定している。PBFは以下①~④のプロセスを何度も繰り返すことにより部品を製造する手法である(Fig. 2)。
① 造形エリアのビルドピストンを降下させ、粉体材料を敷くための間隙をつくる
② パウダーフィードピストンを上昇させ造形エリアに供給する粉体材料を押し上げる
③ 押し上げた粉体材料をレベリング・ローラーにより造形エリアに搬送する
④ 造形エリアにレーザーを照射し材料を溶融・固化させる
現在、PBFの生産性・設計自由度・材料自由度の高さを活かし、部品の試作・量産を行っている。
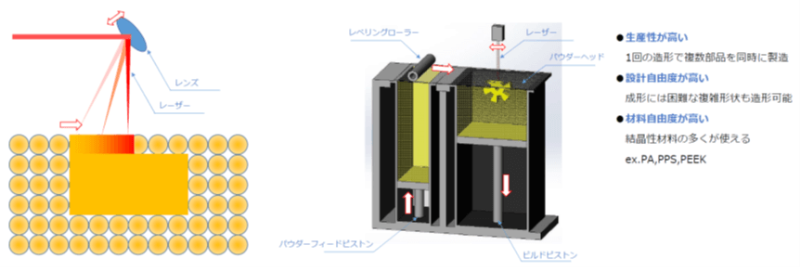
Fig. 2 Additive Manufacturing Process (Powder Bed Fusion(PBF))
3
AM技術開発
3.1 生産面での技術取組
3.1.1 造形精度向上技術
プロフェッショナルプリント製品は高精細な印刷品質が求められる精密機器であり、構成部品は高い要求精度を確保する必要がある。AM部品の適用拡大を図るためには造形精度を向上させる必要があり、今回平面方向寸法精度及び高さ方向寸法精度について精度改善を試みた。
(1)平面方向寸法精度
平面方向の寸法精度はレーザーの照射位置精度の影響が大きい。これまでは目視判定によりレーザー照射位置を確認していたために、レーザー指令位置と実際の照射位置とのズレを定量的に評価しておらず、正確な照射位置補正ができていなかった。そこでCNC画像測定器により照射位置ズレ量を正確に求め、レーザー座標補正を行うことによりレーザー照射誤差を大幅に改善した(Fig. 3)。
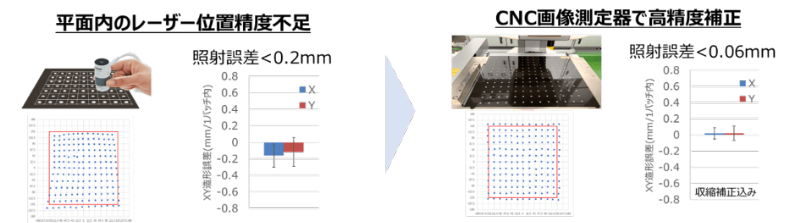
Fig. 3 High-Precision correction using CNC Image Measuring Machine
(2)高さ方向寸法精度
PBF方式のAM装置では、造形エリアの温度バラつきが寸法影響因子であることが分かっており、造形位置によって寸法バラツキが生じる。具体的には造形エリア外周部に対し中央部のZ寸法が顕著に小さくなることが寸法精度上の課題であった。そこで、温度分布不均一の原因と推定された装置内の高温部から低温部への熱伝導に対し、造形エリアを加熱するヒータを中心に計9か所のヒータ温度条件のチューニングによる改善を試みた。結果、条件変更前と比較し大幅に寸法精度バラつきの改善効果を確認した(Fig. 4)。
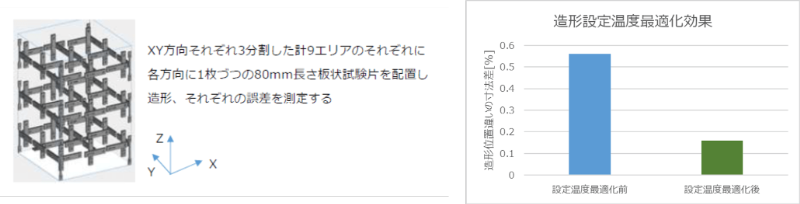
Fig. 4 Improvement of variation by temperature tuning
3.1.2 コスト削減のための材料リサイクル率向上技術
AMで使用される材料は現状では普及率や製法等が原因で高額となっており、AM部品費の材料費が占める割合が非常に高くなる。これによりAM部品の量産適用の阻害要因となっていた。その解決策としてAM材料のリサイクル率に着目した。AM材料のリサイクルとは、造形時にレーザー照射されていない部分を次回以降の造形に材料毎に定められた比率で混ぜることである。この比率(リサイクル率)は材料固有の熱的安定性によって0%~80%程度まで幅があり、実質的に材料費を定める因子となっている。このリサイクル率を向上させることにより、AM生産部品のコストダウンを進めてきた。
プロフェッショナルプリント製品の部品には難燃性が求められるケースが多いことから難燃剤含有ポリアミド12を使うこととしたが、この材料は推奨リサイクル率が20%と低く材料リサイクル率を向上させる技術を開発した。
単純にリサイクル率を向上させると、稜線が荒れる、表面粗さが悪化する、ヒケが大きくなる、強度が低下するなどの造形不良が発生してしまうことがわかっている。この原因を特定するために各種分析を実施したところ、造形によって材料にかかる熱履歴がポリアミドの分子間架橋を促進したことで分子量が増大し、熱的流動性が低下することによって溶融時のメルトプール(=溶融樹脂溜まり)が広がりづらく、造形品外観の悪化の原因となることが分かった。(Fig. 6)。その状態の材料で高品質に造形を完了させるため種々の検討を実施した。
現在までに確認されているリサイクル率向上に有効な手段としてレーザー出力の向上が挙げられる。先に述べた通り、リサイクル率が高い材料は架橋が進行しているPAが多量に含まれており、レーザーが照射された際も濡れ広がりづらい。特に造形品側面のヒケが顕著で、溶け広がっていない場合はヒケ量が大きくなり造形不具合となる。レーザー出力を上げることによって材料溶融が促進しヒケ量が小さくなることを確認している。実際に、リサイクル率を20%から60%に上げた時、Fig. 7に示すようにレーザー出力を基準値より32%向上することで、ヒケ量が同等になることを確認している。
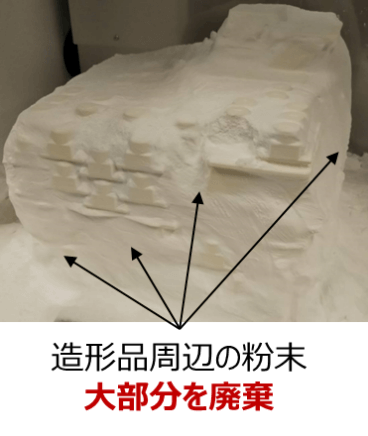
Fig. 5 Appearance Immediately after printing
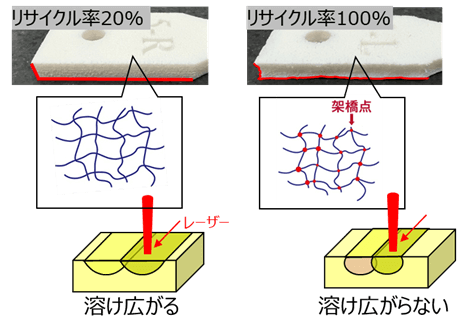
Fig. 6 Effect of difference in recycling rate on printing results
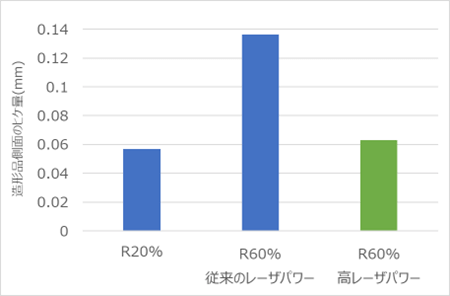
Fig. 7 Variation amount of printing error after laser power optimization
3.2 設計面での技術の獲得
3.2.1 高い設計自由度を活かした機能部品への展開
AMは形状自由度の高さが強みと言えるが、一方でその設計手法はまだまだ確立されていない状況であった。そこで成形加工や板金加工では実現不可能な複雑形状への対応が可能である利点を活かし、機能観点で最適化された設計手法を検討してきた。その検討事例について紹介する。
(1)冷却エアフロー部品の最適形状設計
形状自由度の高さを活かし機能が向上した事例として冷却エアフロー部品の事例を紹介する。この部品は限られたスペースの中で風速を向上することが求められるものである。CAEで冷却効率が最適となる形状を自動探査した結果、従来と大きく異なる曲面を駆使した形状デザインが最適であることを導出した。結果として平均風速は1.52m/sから2.23m/sと46%向上する効果を得ただけでなく、部品点数を減らしコスト削減効果を得た(Fig. 8)。
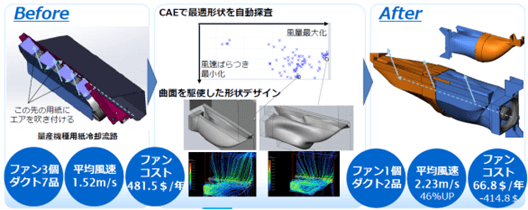
Fig. 8 Optimal shape design of cooling airflow parts
(2)軽量性と高剛性を両立する設計
軽量性と高剛性を両立するための構造として、Fig. 9に示すハニカム形状やラティス構造が有名である。特にラティス構造は他の製造手法で採用することは現実的ではないがAMを用いれば容易である。例えば重量が大きくなる大型部品であれば組立性やメンテナンス性に有用であり、動作させる機構部品であれば省力化へと繋がる。
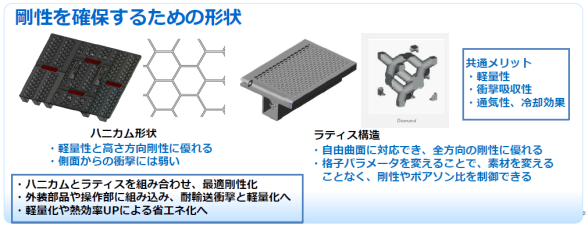
Fig. 9 Designed to achieve both lightness and high rigidity
3.2.2 生産コストに配慮した設計
生産コストに占める割合が高いのは部品製造コストと組立コストである。前者の部品製造コストはPBF方式AMにおいては造形エリアに可能な限り多くの部品を配列し生産効率を向上することにより低減する。後者の組立コストは部品一体化による組み立て工数の削減が挙げられる。
(1) AM生産効率に配慮した設計
1回あたりの造形コストは材料費が支配的であり概ね造形高さにより決定する。即ち、造形高さを維持したまま生産できる部品の数が2倍になれば1個当たりの部品費は1/2になると考えて良い。造形エリア体積中に占める部品の体積割合を充填率と定義する。充填率を高めるためには無駄なスペースが無い部品形状が好適となる。箱型の部品は可動構造を持つ部品に設計変更し、展開状態で造形することで部品製造原価を78%削減することができた。また、組立時にセットとなるような部品が存在した場合、造形配列時の無駄なスペースが無くなるよう重ねられる形状に修正したり、組合せである部品の内部に別の部品を配置できるようにしたりすることで部品製造原価を61%削減した。(Fig. 10)

Fig. 10 Designed for AM production efficiency
(2) 部品一体化設計
組立工数削減を狙いとした設計事例として用紙整合機構部品を紹介する(Fig. 11)。この部品は他の生産手法で製造する前提で設計していたため、部品点数は22品となっていた。部品の一体化を極限まで引き上げつつCAE解析による強度解析、機構解析を行った結果、部品数は4品まで減らすことが可能であることを確認した。
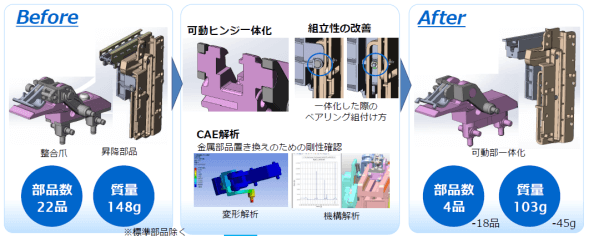
Fig. 11 Parts integration design
4
まとめ
プロフェッショナルプリント製品の部品をAM生産に置き換えることを目的として、生産技術・設計技術の両面からのアプローチにより部品に要求される機能及びコストの両立を図れる可能性を明確にした。その結果として2022年度から本格的に量産展開を開始している。今後その生産規模を高めるため更に造形品質を向上させつつコストを低減させると共に、設計技術向上による付加価値の高い部品の開発を進めていく。
AM生産技術は事業領域を超えた部品提供が可能なため、コニカミノルタにおける主要な生産技術として育てていくことを目指し、その延長線上にはAM生産のノウハウを持たない社外に対し部品提供という形でソリューションビジネスを展開することで、社内だけでなく製造業全体のエンジニアリングチェーンとサプライチェーンを変革していくことを最終目標として今後、更に貢献の幅を増していく。