1
Overview
Since the launch of the 8050, a high-speed digital color MFP, in 2003, Konica Minolta has developed and deployed production printing machines using electrophotographic technology. At print-on-demand shops, easy-to-handle printing machines with accurate and stable color reproduction performance play a key role. We developed the Color Density Control function, which renders color patches on the print paper, conducts measurement using the inline color sensor, and controls and maintains the target tone. We also developed the Auto Image Adjustment function, which detects the color changes during printing processing based on tiny patches on the print paper using the IQ-501 and performs the Color Control in real time, as discussed below. The function is incorporated in Heavy Production Printers (HPPs) for commercial printing as well as Mid Production Printers (MPPs) and Light Production Printers (LPPs). We continue to develop technologies and products with the aim of achieving ease of handling and high quality. This paper introduces a new color correction technology, Intelligent Color Control, incorporated in the latest models: the AccurioPress C14010/12010 and the IQ-601.
2
Details
■Configuration
To maintain the color printing quality, it is essential to 1) adjust the color shades (gradation) to match the target properties and 2) suppress the color changes during printing. The print density adjustment has two functions. One is the Color Density Correction, which adjusts the basic colors (four YMCK colors) to the designated gradation properties on paper. The other is the Color Control, which maintains the tone after the Color Density Correction, as explained in this paper. In electrophotographic color printing, single colors are overlaid to reproduce mixed colors. However, colors go through complex changes due to the interaction of overlaid colors. ThusTherefore, color correction must also target mixed colors. Conventionally, high-speed processing was achieved by an algorithm that adjusts the shades based on a total of eight color factors: four basic colors, three colors of RGB, which represent mixed colors of two layers, and gray (processed black), which is the mixed color of three layers.
■Function / Features / Applications
Meanwhile, mixed colors entail various change factors, including shades and changes in the hue direction, etc., resulting in inadequate adjustment flexibility. Thus, we devised a solution to flexibly cope with color changes by increasing the number of shade adjustment factors from eight for the conventional system to 13, including overlay interactions. Detailed monitoring of color changes requires frequent measurement and as-required detection. Thus, the number and size of adjustment charts must be minimized. Figure 1 shows the composition of the adjustment chart. a) is for the Color Density Correction with patches of the basic colors rendered. b) is for the Color Control and consists of the basic colors and mixed colors. c) is for the Auto Image Adjustment with two compositions of basic colors (left) and mixed colors (right) rendered in the cutting margin of the print paper.
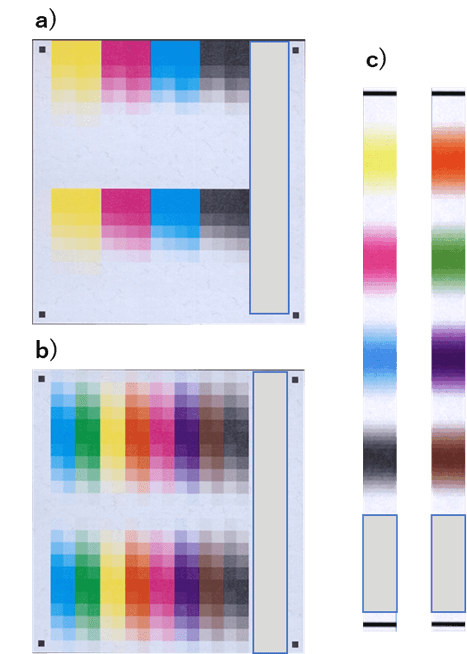
Fig. 1 Diagrams of color chart images.
The part in each design shows the margin for special color (white) measurement. Among all the colors expressed by color printing (color space), only a fraction of colors can be analyzed using these patches. Thus, we used an algorithm to estimate the direction of color changes in the entire color space based on the position (distribution) relationship between the changes in the rendered patch colors and patch colors in the color space, calculate the correction value, and optimize both the correction frequency and accuracy. High-speed printing was realized by processing the data using an ASIC circuit. Figure 2 shows the results of color correction for the testing equipment, which generated color change noise mainly in the hue direction (i.e., an issue of the conventional system), and comparison of color difference (vertical axis: relative value) before and after correction. Compared with the conventional system a), which is highly effective for single colors, the new system b) reduced the color difference by approximately 0.36 times even for mixed colors as in the case of single colors.
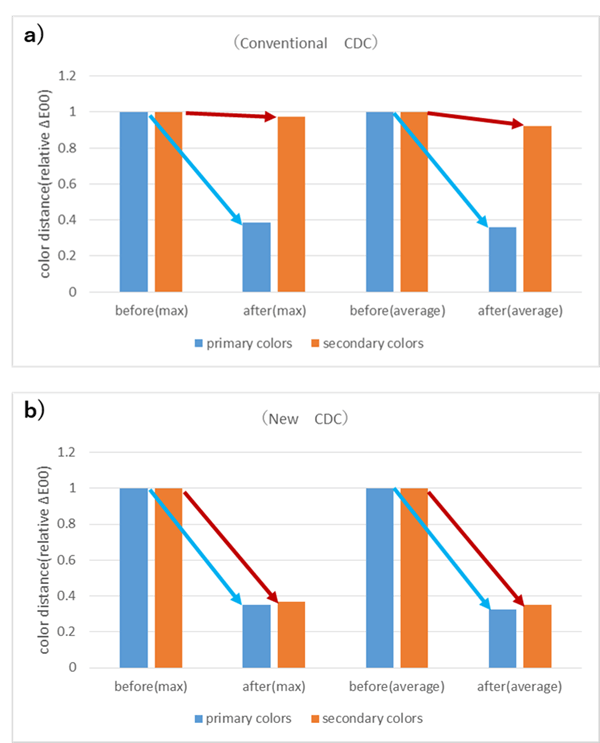
Fig. 2 Comparison of color correction effects.
■Future outlook
As discussed above, we introduced a new color correction technology. Konica Minolta will continue to refine its expertise through on-site observation, develop necessary technologies, and contribute to colorful solutions through on-demand printing.