1
Overview
Konica Minolta aims to achieve a process for conducting virtual evaluation, such as simulation, and refine the functionality and quality before manufacturing products. These evaluation technologies are used in the development of products, such as MFPs. We have been acquiring similar simulation technologies and building a track record for industrial inkjet printers as well.
The inkjet printer using sol-gel phase transition UV inks (Fig. 1) realizes high image quality by properly controlling the temperature of inks and printing media and the ink jetting. Notably, the media temperature is affected by the temperature control in the transport unit, ink temperature and UV hardening. Thus, a technology to predict the series of phenomena is the key. In image formation, we developed a technology to simulate the behavior in which ink droplets placed on media come into contact with each other and become bonded. This paper introduces these technologies and discusses the future outlook.
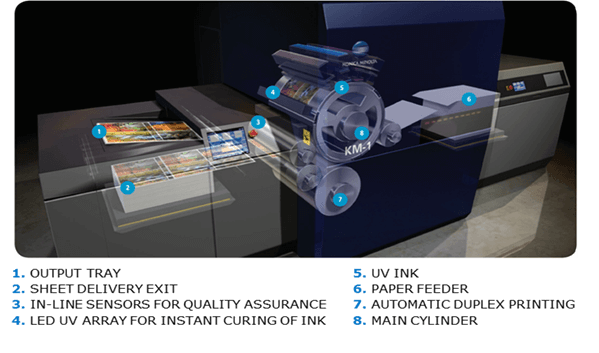
Fig. 1 System of digital inkjet pres AccurioJet KM-1
2
Details
■Configuration
Figure 2 shows the correlation between the designs and simulation technologies directly related to the image quality in the inkjet field. These simulation technologies are introduced.
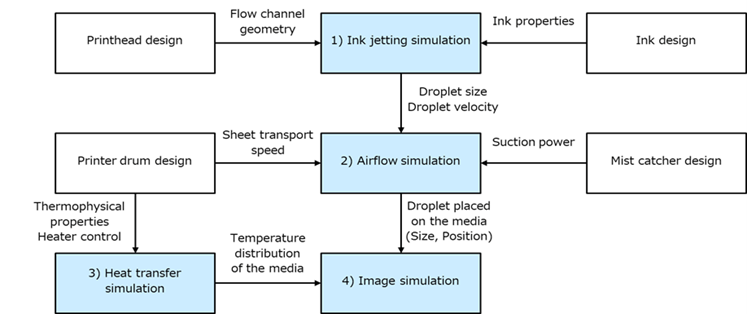
Fig. 2 Simulation technologies relating imaging process.
■Functions / Features / Applications
1) Ink jetting simulation technology
Based on this technology,1) we created a model of the generation of satellites and mists attributed to changes in the ink pressure in the IJ printhead caused by driving waveforms applied to the piezoelectric actuator, jetting of ink droplets, and break-ups and collisions of ink droplets in the air (Fig. 3). This made it possible to extract design parameters which minimize the generation of satellites and mists. This model achieves both high accuracy and low calculation cost by combining the computational fluid dynamics (CFD) model, which predicts the ink droplet formation process, with the 1DCAE model, which expresses the changes in pressure that affect inks (Fig. 4), and by introducing a model capable of evaluating the surface tension accurately.2,3)
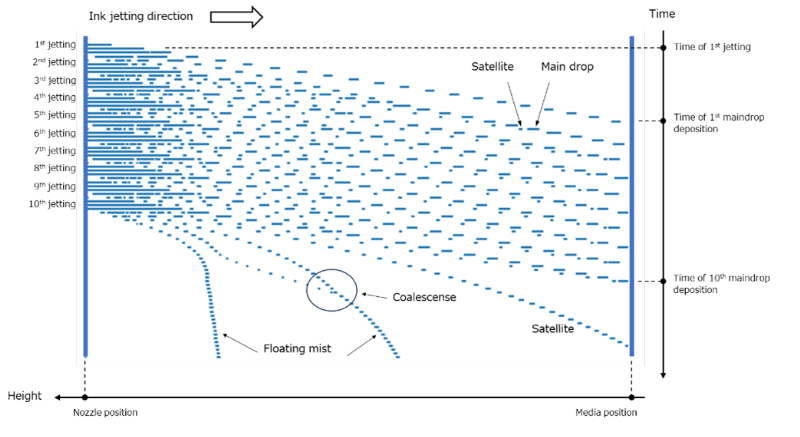
Fig. 3 Change in positions of ink droplets ejected 10 times in succession.
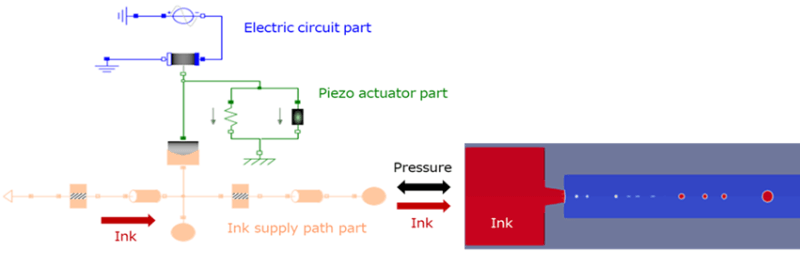
Fig. 4 Schematic diagram of cooperation between CFD model and 1DCAE model.
2) Airflow simulation technology
The trajectory of ink droplets due to the airflow generated by the media transfer is calculated based on the data of the liquid amount and the velocity of ink droplets obtained in the ink jetting simulation. The displacement amount of the placing position is calculated for main droplets and satellites placed on the media to evaluate the impact on the image quality. Additionally, mists that are not placed on the media are tracked to calculate their adhesion and collection sites after floating, which allow us to assess mist contamination within the system and collection efficiency (Fig. 5).
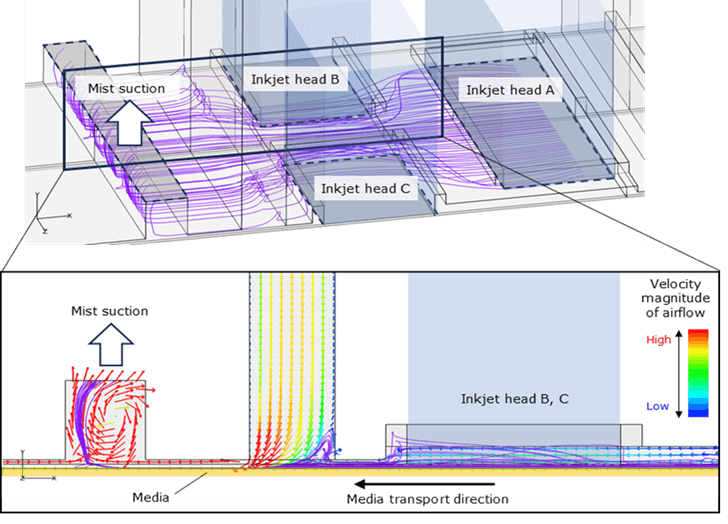
Fig. 5 Calculated trajectories of mist (violet line) and velocity of airflow (arrow).
3) Heat transfer simulation technology
The media temperature during printing is predicted by taking into account the heating of media, temperature drop, and temperature rise by exposure to UV rays during transfer. This technology is used to design the heating/cooling mechanism for temperature control and build the control system (Fig. 6).
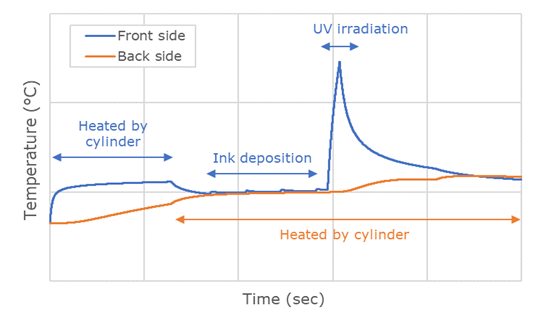
Fig. 6 Temperature changes of media during transport
4) Image simulation technology
In this technology, the ink droplet placement position and liquid amount are received from the airflow simulation, and the media temperature is received from the heat transfer simulation to output the final predicted images (Fig. 7). The previously used technology4) was not suitable for high-density images. Thus, we developed an algorithm to repeat transformation prediction at short intervals using a regression formula (Fig. 8). The movement of each point on the boundaries of ink droplets in one step is predicted based on the condition near the point. Because the algorithm does not depend on the condition of a wide area, such as the image density, it can also be applied to high-density images in addition to low-density images. Compared to CFD analysis, the algorithm can handle a large number of ink droplets because the calculation time is very short. Thus, it is used to design the image processing, including missing nozzle compensation.
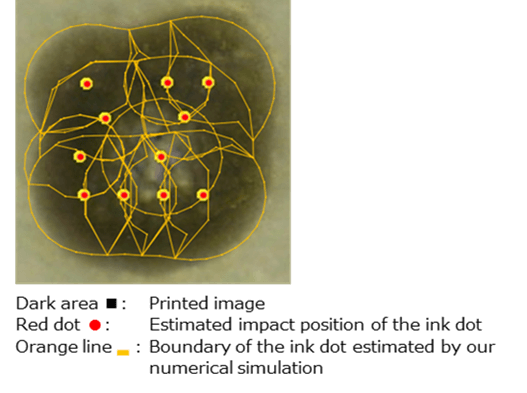
Fig. 7 Comparison between a printed image and the estimated dot boundaries.
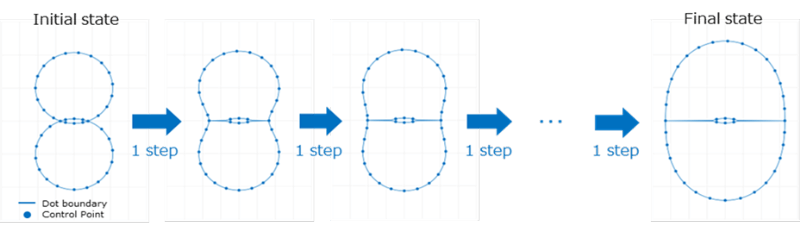
Fig. 8 Time evolution of estimated dot boundaries.
■Future outlook
We have introduced a series of simulation technologies to reproduce the printhead jetting and ink behavior on media. We will continue to deploy this initiative and advance the process to enhance the functionality and quality before manufacturing products. We remain committed to helping refine products, including the AccurioJet 60000 next-generation inkjet printing machine.