1
Overview
Konica Minolta has engaged in the business of polarizer protection films and optical compensation films using cellulose-based materials for the display market. We developed the SAZMA next-generation acrylic films in response to the larger display size, water resistance and optical stability requirements to meet the needs for high durability in the mobility field, and growing expectations for water-resistant materials that can replace cellulose-based materials in recent years. The SAZMA films are characterized by ease of surface processing and optical isotropy, which are achieved by the proprietary formulation design and process design and which cannot be attained by conventional acrylic films. As a result, the products provide development designers at user companies with flexibility in surface processing and design change, including the display panel configuration. The SAZMA films are also designed to effectively utilize resources, contributing to higher productivity and lower environmental impact through the supply chain. Initiatives are under way to apply the films to various cutting-edge displays in addition to polarizers.
2
Details
In the previous report, we reported the SAZMA concept.1) In this report, we introduce two types of SAZMA films. One is the SAZMA-S, a base material for surface protection developed mainly for polarizers, and the other is the SAZMA-Z, a base material with zero retardation. The main physical properties are shown in Table 1 below.
Table 1 Specifications of SAZMA film.
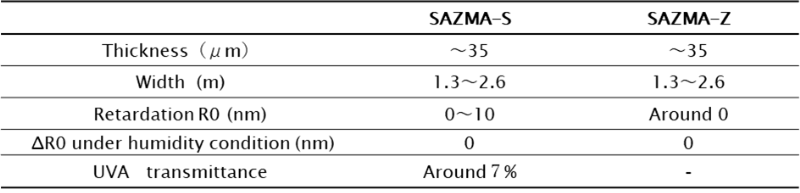
Introduction of Konica Minolta’s film casting process
There are two main polymer film casting methods: the solvent-cast method and the melt-cast method (Fig. 1). The solvent-cast method is further classified into two types: the drum type and the belt type. Konica Minolta uses the belt type of the solvent-cast method, which has the following characteristics.
・Polymers with high molecular weight can be used. The low-temperature processing enables the selection of heat-sensitive additives.
・Unnecessary scrap film generated during production can be dissolved for recycling.
・It is easy to control the drying time after casting, which is an advantage in reducing the film thickness.
Additionally, films produced using the solvent-cast method are designed to accommodate widths exceeding 2.5 meters by post-stretching.
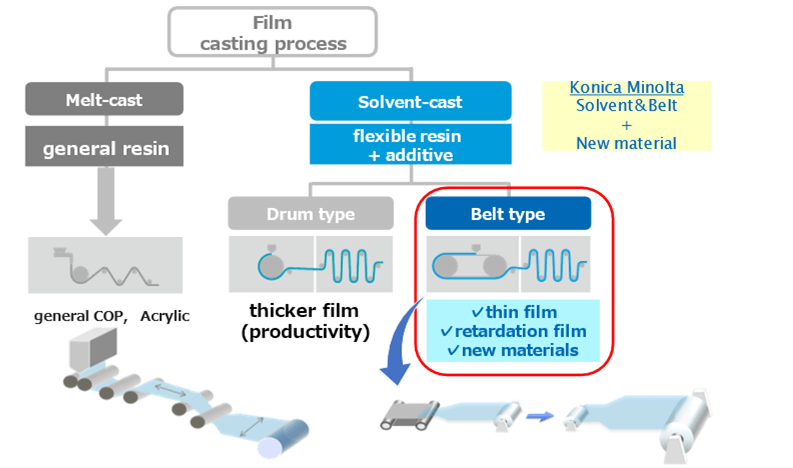
Fig. 1 Three different casting processes.
■Function / Features / Applications
The SAZMA films have overcome the difficulty of handling, which is a disadvantage of conventional acrylic films. They have the following characteristics due to materials and additive technologies and process improvements.
・The surface energy is high. The surface is smooth and easy to process. The base material is flexible. The resilience is about 1.8 times that of conventional acrylic films (Fig. 2).
・The stress birefringence is kept low. The retardation does not change due to external force. Mura (non-uniformity) does not occur when the films are embedded in display systems (Fig. 3). The base material is characterized by low retardation. Thus, no interference fringe or rainbow mura occurs when combined with various types of backlighting.
Thus, the films enhance the flexibility of the surface processing design, including coating and debossing by developers, and the design of panels embedded in display systems, which is the downstream process.
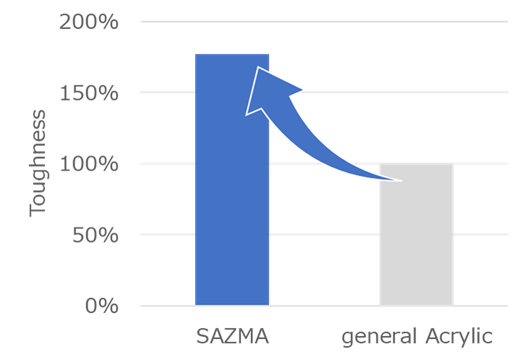
Fig. 2 SAZMA is much more tough than general Acrylic.
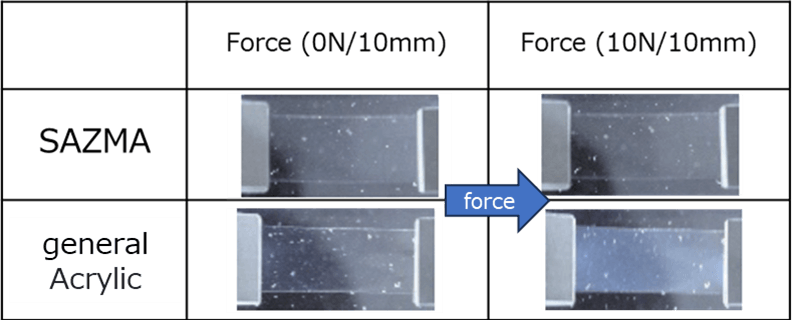
Fig. 3 Observation in a cross-Nicols State.SAZMA has low photo-elasticity and does not show any non-uniformity even when stress is applied.
The SAZMA films are designed to minimize changes in the roll shape, thus contributing to long-term storage performance and production efficiency at production sites.
■Future outlook
The SAZMA films have been deployed in stages for polarizers. They are designed to demonstrate optimal performance when laminating the SAZMA-S, which is a base material for surface protection via a polarizer, with the SAZMA-Z, which is a base material with zero phase difference, or with SANUQI,2) which is our optical compensation film (Fig. 4). The use of top and bottom films with the same width and roll length using long sheets helps reduce the processing loss in the lamination process, thus further improving productivity and reducing the environmental impact at customers. Applications for various state-of-the-art displays, in addition to those for polarizers, have been expanding by utilizing the optical isotropy and the potential of reducing the film thickness.
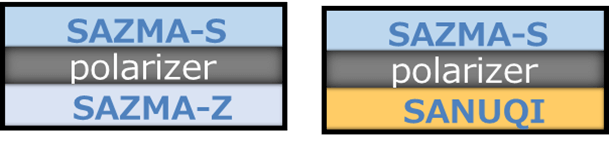
Fig. 4 Sectional views showing structures of a polarizing plate.