Air cushioning system technology
Significant reduction in use of packing materials by using airbags with a proprietary structure
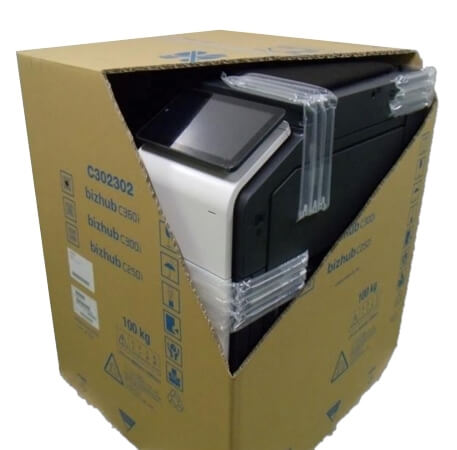
The amount of resin materials used as packing materials has been reduced significantly by replacing blocks of conventional foamed resins with airbags having a proprietary structure.
In general, polystyrene foam is used as a cushioning material to mitigate the impact on products during transport. Conventional cushioning materials are bulky and inefficient: they take up space, incur transport costs, and have an environmental impact in all the processes, including manufacture and transport, packing of products, delivery to customers, and collection and disposal.
Konica Minolta has developed a proprietary air cushioning system that efficiently reduces impact. The system has been used for heavy objects, which were previously difficult to protect using conventional air cushioning materials.
In this system, the necessary amounts are cut and attached to the necessary areas. This eliminates the need to form cushioning materials into special shapes for respective products in large amounts in advance, thereby helping reduce inventory.
Technology Overview
Conventional air cushioning materials have a simple bubble structure wherein each air unit (cell) is independent, and so are damaged if air is suddenly compressed by a large impact. Increasing the elastic force impairs the cushioning performance.
Konica Minolta’s new air cushioning system has a structure in which two cells are interconnected and compressed air in an impacted cell moves into the other cell. This structure mitigates damage to products when airbags are damaged or the pressure increases suddenly. The shape of the interconnecting pathway is designed to increase the efficiency of converting impact into heat, achieving a high cushioning function with a compact system.
This technology has reduced the volume by 84% (and weight by 70%) compared to conventional polystyrene foam cushioning materials. Heavy objects of 200 kg can be protected by reducing the cushioning distance from 35 mm, which is required for conventional cushioning materials, to 20 mm. In FY2020, Konica Minolta started to use this technology to pack its MFPs. Previously, packing 260 MFPs required two four-ton truckloads of cushioning materials, but this can now be replaced by a single roll of this system of 500 mm in width and 280 mm in diameter.
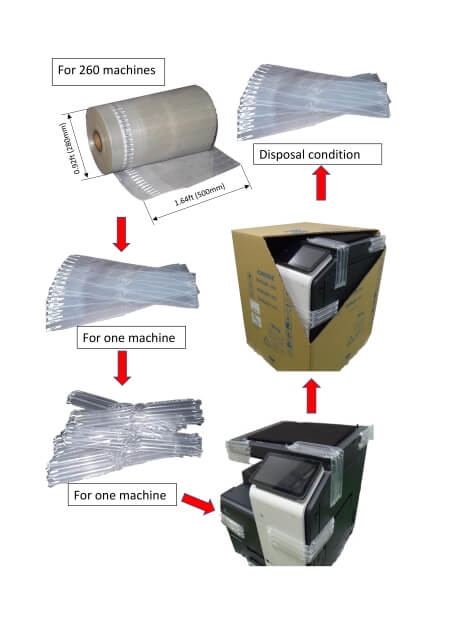
Roll-shaped airbags are cut into necessary amounts. They serve as cushioning materials by filling them with air and attaching them to products.
Greatly reducing the volume of packaging materials in warehouses
The volume is 1/100 or less that of polystyrene foam. Cushioning materials which filled a warehouse can be replaced by a single roll (500 mm in width, 280 mm in diameter).
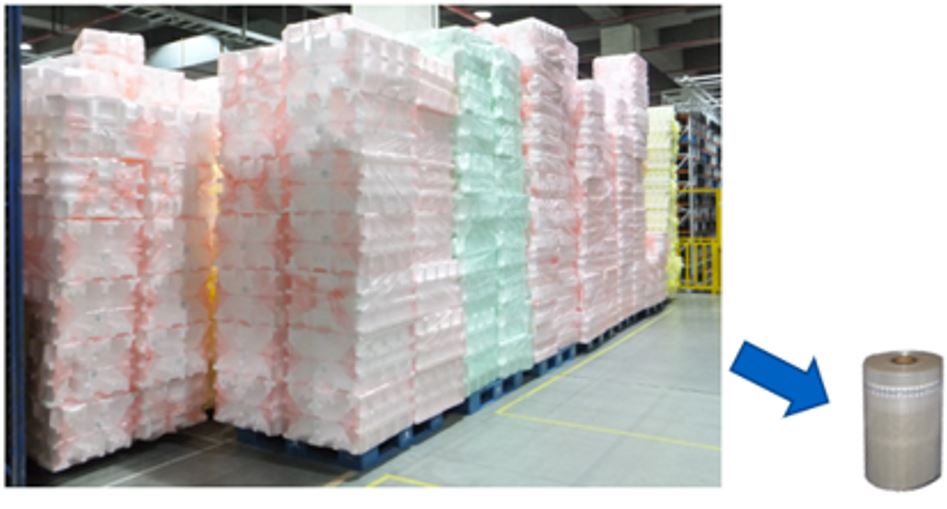
(Left) Conventional polystyrene foam cushioning material
(Right) Cushioning material using the new air cushioning system
Highly versatile packing material
The number and arrangement of airbags can be optimized for products of different sizes, shapes, and weight.
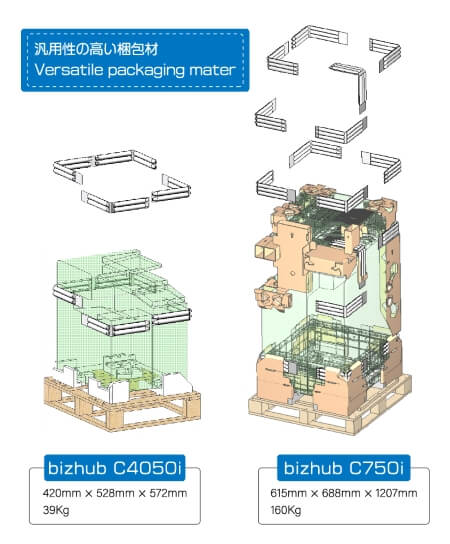
Award-winning history
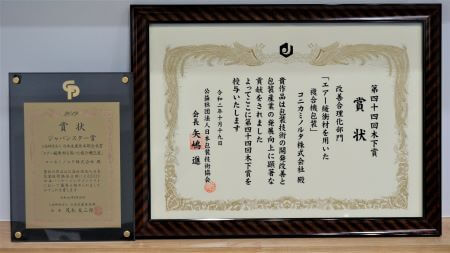
In FY2019, Konica Minolta won the Japan Star Award (Japan Productivity Center Chairman’s Award), which is the most prestigious award in the packaging industry, from the Japan Packaging Institute (JPI). In FY2020, the company won the 44th Kinoshita Award, which is presented to those who made great progress in improving and rationalizing packaging, from JPI.
Category to which this technology applies
(click to see a list of technologies in that category)
\Our expert team handles inquiries
on technical partnerships and joint research./