Technology for performing maintenance and remote diagnosis to identify signs of defects in printed image quality
Self-monitoring and restoration of image quality by presses to maximize the operating time
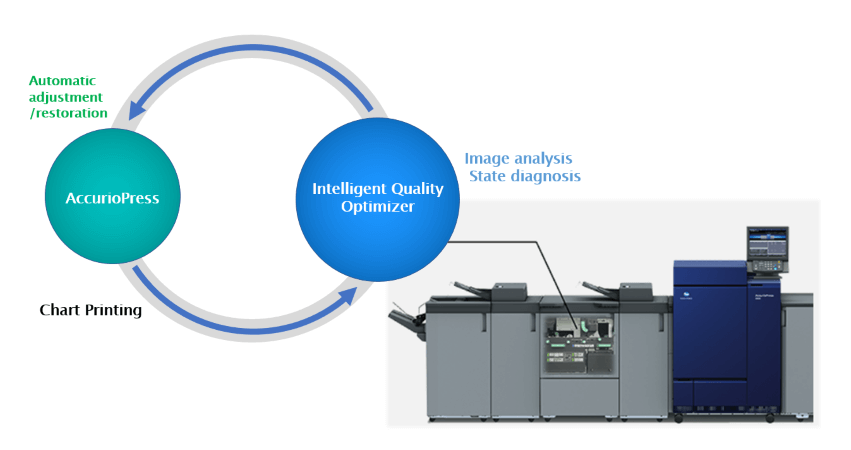
Enable predictive action and advance diagnosis of components requiring maintenance in workplaces without overlooking changes in image quality, and maximize the operating time
In commercial applications, quality defects force customers to suspend printing operations. To quickly solve problems with image quality, which is a key concern for customers, we have developed a system called Auto Quality Adjustment (AQA) which combines an image diagnosis technology and an automatic restoration function. This system regularly monitors the state of images and locates the causes of image problems, enabling presses to restore image quality. Furthermore, by remotely monitoring the diagnosis results and detecting signs of problems, maintenance work by customer engineers (CEs) on customers’ premises can be optimized, helping to maintain the quality of printed matter and maximizing the operating time of presses.
Technology Overview
The printed image quality diagnosis system automates the isolation of image problems, which conventionally has been performed by CEs. It prints and scans charts for measuring the quality of printed images, and quantitatively evaluates image noise inherent in presses, such as streaks, spots, stains, and uneven density. Moreover, the system makes AI link quantitative evaluation results of image noises with image problems occurring on presses and learn from them, so that presses can locate those parts that are causing problems through self-diagnosis. AQA realized by combining AI for image diagnosis will revolutionize after-sales services in the printing business.
Technology for quantitatively evaluating printed image quality
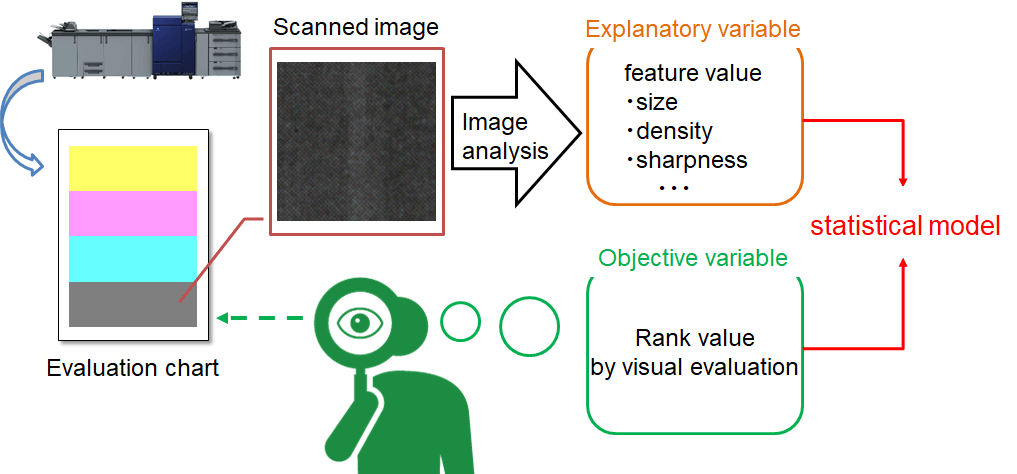
Technology for quantitatively evaluating printed image quality based on image analysis and statistical model
The digitization and quantitative evaluation of the state of images of presses has been an issue in performing maintenance at appropriate timing. We studied this issue, used a statistical model to analyze the relationship between the image features extracted by image analysis from the scanned images of printed evaluation charts for measuring image quality and the visual evaluation values of images, and developed a technology that can quantify the degree of image noise. With this technology, which accurately mimics the visual characteristics of the human eye, the state of images of presses can be remotely monitored.
Diagnosis of parts requiring maintenance by using the results of quantitatively evaluating printed image quality
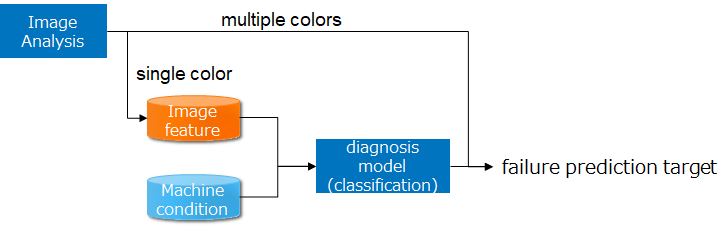
Example of model for diagnosing parts requiring maintenance created based on image features and printing operation data
We have developed a technology that locates parts that are causing image problems and require maintenance from image features analyzed by the IQ-501 (Intelligent Quality Optimizer) and data on the operating state of the press. This technology uses a classification model based on machine learning to learn the relationship between the results of quantitatively evaluating printed image quality and past image problems based on data collected from many presses operating in the market. By combining this image diagnosis technology with the abovementioned image state monitoring, our system enables CEs to perform predictive maintenance promptly before customers suffer image defects. We are now working on expanding the range of target parts.
Category to which this technology applies
(click to see a list of technologies in that category)
\Our expert team handles inquiries
on technical partnerships and joint research./