Thin layer coating technology for optical parts
Imparting desired characteristics by forming a functional thin layer
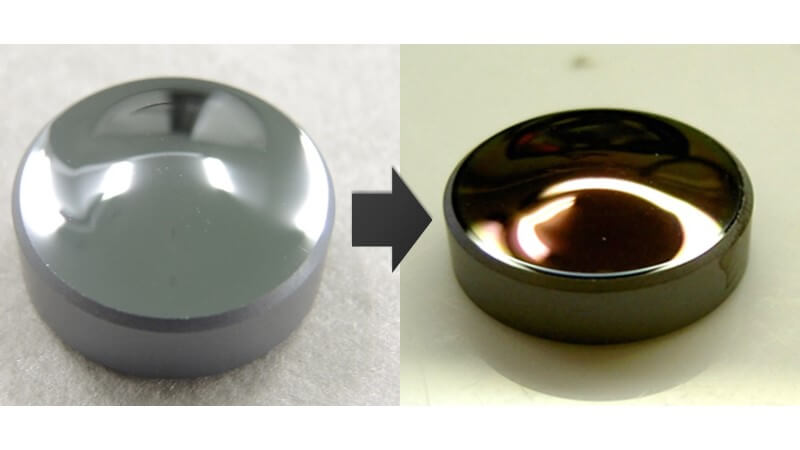
Optical performance is improved by forming a thin layer depending on the required function.
To improve the output quality of an optical system, it is necessary to optimize the characteristics of the constituent optical parts and materials. Konica Minolta is adept at controlling the characteristics of optical parts and materials by utilizing both optical coating design and vapor deposition technologies.
For example, an anti-reflection coating improves the quality of image sensing by suppressing light loss, ghosting, etc.
In addition, a band-pass coating, which reflects light of a specific wavelength, selectively allows light to pass through it, thus improving the accuracy of images projected by projectors etc.
Through our optical coating technologies, Konica Minolta is helping to enhance the performance of optical parts and materials and improve the accuracy and quality of optical apparatus.
Technology Overview
Vapor deposition coating technology involves evaporating or sputtering a material and depositing it as a thin layer on a substrate, such as glass. The formed metallic layer adjusts the light transmittance, light reflectance, etc. and gives optical parts and materials various characteristics.
Konica Minolta handles optical coating with diverse functions, such as anti-reflection coating, band-pass coating, protective hard coating, and anti-fogging coating.
These diverse optical coatings are the result of Konica Minolta’s simulation tools and library of formulas and materials which it has developed and accumulated through decades of producing optical products. By making the most of these tools and multiple coating processes, Konica Minolta provides high-quality, high-reliability coatings as well as optical parts and materials to meet the needs of society.
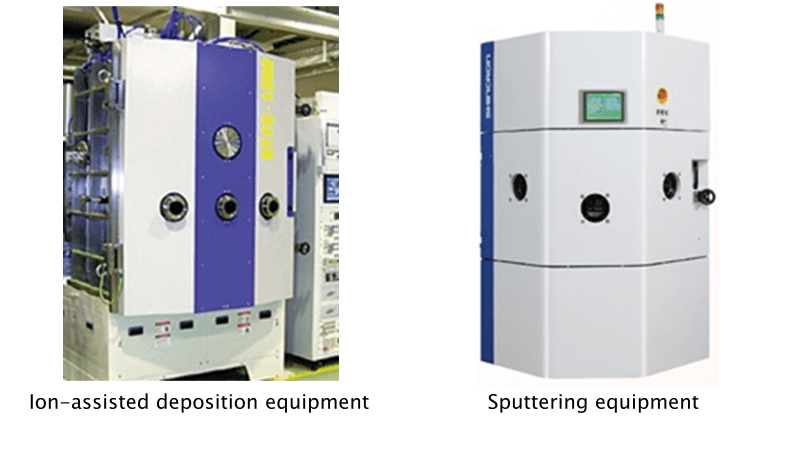
Ion-assisted deposition equipment for multi-layer coatings /Sputtering equipment for multi-layer coatings
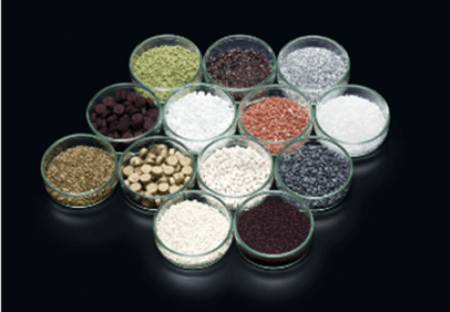
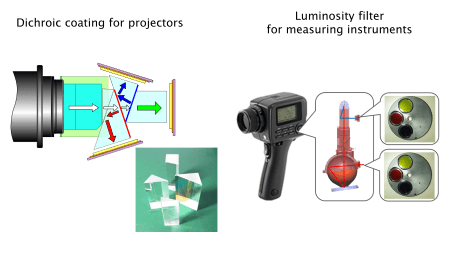
Materials for optical coating
Application examples of products (dichroic coating for projectors/luminosity filter for measuring instruments)
Products and services that use this technology
Category to which this technology applies
(click to see a list of technologies in that category)
\Our expert team handles inquiries
on technical partnerships and joint research./