Real-time printed image analysis technology
Automatic image adjustments by machines to always offer printing output under optimal conditions
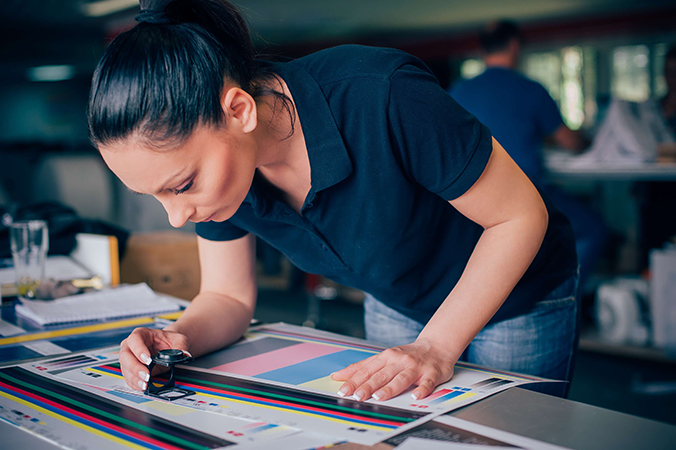
Konica Minolta’s technology performs the image adjustment process and the printed material inspection process, both of which require the “hands” and “eyes” of the operator, thus reliably maintaining the quality of printed matter.
At printing worksites, adjustment of the colors and their density and printing positions, inspection of products, etc. rely on the skills and know-how of experienced operators. Sometimes, printing cannot be performed because adjustments must be made.
The IQ-501 (Intelligent Quality Optimizer) automates these operations with the aid of Konica Minolta’s original technology, enabling anyone to perform printing efficiently and easily. The reduction in work time increases the operating time of the printer, improves production efficiency, and boosts customers’ business.
Furthermore, the IQ-501 frees printing worksites from having to rely on skills and experience, freeing up staff from diverse fields to work in various styles, such as part-time.
With the IQ-501, Konica Minolta is helping to create pleasant printing worksites where anyone can produce printed matter of higher quality than imagined.
Technology Overview
A printing device occasionally causes variations in colors and printing positions due to environmental conditions such as temperature and humidity, so operators have had to adjust colors and printing positions appropriately before or during printing. They also check each sheet of printed matter after printing.
The IQ-501 is equipped with scanners that can read the entire area of paper and a spectrophotometer for accurately measuring color. This combination enables customers to constantly scan images while printing, reduce the chrominance ⊿E00 between the start of printing and any point during printing through real-time corrections, and inspect printed matter for defects such as micron-order stain.
The IQ-501 helps solve issues that customers have long assumed they had to fix, by combining various imaging, measurement, optics, and machinery technologies.
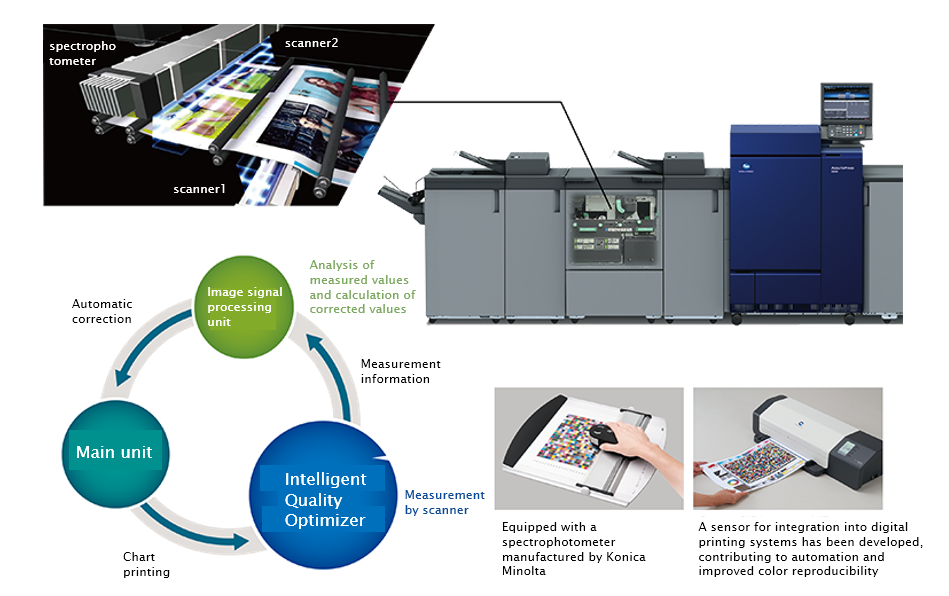
Printing system integrating the IQ-501
Automatic adjustments provided by the IQ-501
Optimal high-accuracy paper transfer technology for scanning
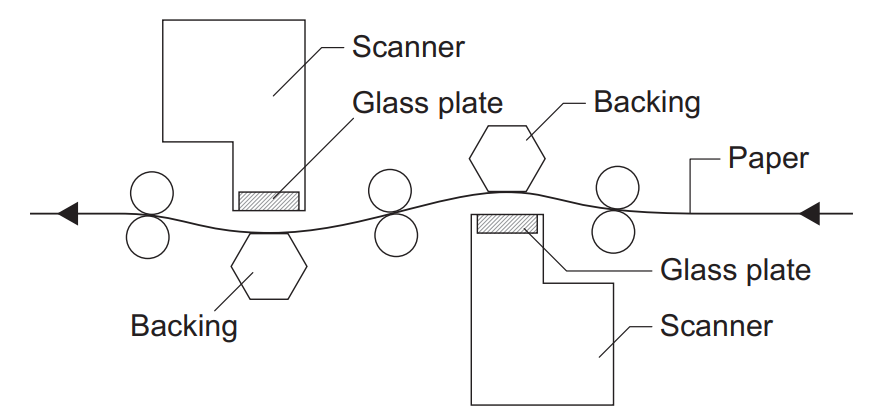
Paper feed path around the scanners
To stably read the colors of printed matter by the scanners, the distance between the paper and the scanners must be kept constant to stabilize the illuminance of the LED lighting on the paper. To achieve this, the transfer path of the IQ-501 is designed to bend the paper at the reading position of the scanners to prevent waviness of the paper, and minimize variations of the distance between the paper being read and the scanners by guiding the paper along the outside of the bending. In addition, to correctly read the printing position relative to paper, it is important to keep transferring paper at a constant speed to prevent images taken by the CCD sensors from shrinking. Thus, the speed of the rollers is controlled to increase along the feed direction toward the downstream side, thus preventing paper deflection in the feed direction inside the transfer path, and the paper is constantly scanned under tension. Thanks to all this, the difference in the speed of paper read by the two scanners can be kept below 0.1%.
Real-time image adjustment technology
High-accuracy position and color tone adjustment technology that does not interrupt printing
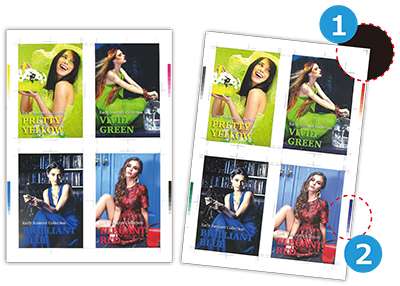
① Pattern for positional adjustment, ② Pattern for color adjustment
As the state of the printing device changes during printing, printing misregistration occurs on the front and back sides of paper in duplex printing. High positional accuracy on the front and back sides of paper is required for commercial printing, and it is therefore necessary to adjust printing positions by detecting misregistration that occurred and feeding it back to printing data. The printing device prints a pattern for positional adjustment in the margin of the printing paper, and the difference between the position of the printed pattern and the target position of the pattern for positional adjustment is detected at any time from the image scanned by the IQ-501 in real time during printing. When the detected difference is fed back to printing data, the IQ-501 calculates a correction value by referring to the printing results on multiple sheets to extract the tendency of misregistration over time, and can thus perform stable adjustments on all pages. Color variations are also adjusted by printing a pattern for color adjustment and detecting the difference between the pattern and the color reproduction at the time of the pre-printing printer calibration (color adjustment) from the scanned image. The IQ-501 achieves high-accuracy color adjustments with the aid of an algorithm, which not only adjusts single colors of CMYK toner for digital photos but also monitors and adjusts variations of mixed colors using two-color or three-color toner.
Hybrid colorimetric technology
Colorimetric technology that ensures short-time, high-accuracy measurement utilizing the advantages of a spectrophotometer and CCD sensors
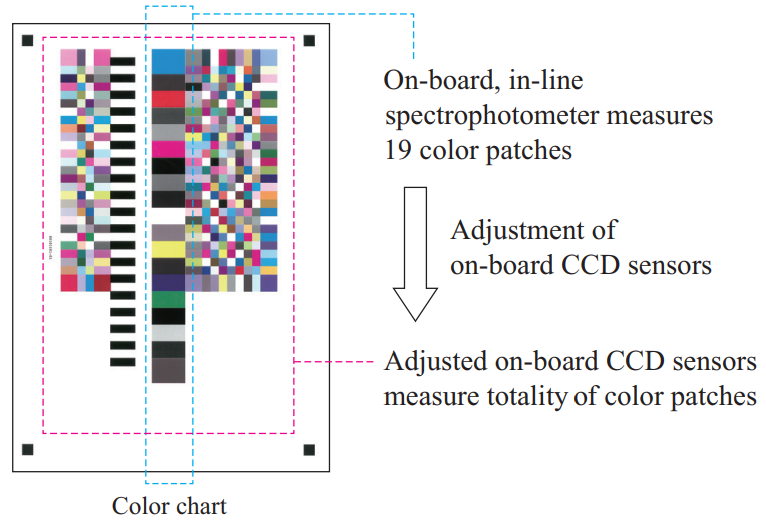
Chart for hybrid colorimetry
Accurate colorimetry of color patches on paper is required to perform color management and thus print the colors as desired by the customer. To obtain accurate colorimetric data, a spectrophotometer is installed in the IQ-501. A spectrophotometer ensures accurate colorimetry but takes time to measure many patches due to its narrow measurement range. On the other hand, a CCD sensor has a wide measurement range and can measure many patches at a time. However, it cannot produce accurate colorimetric data because the data is affected by variations of the sensor and the characteristics of the paper. To resolve these issues, Konica Minolta has developed a hybrid colorimetric technology, which utilizes the advantages of a spectrophotometer and a CCD sensor and can perform accurate colorimetry of many patches at a time by correcting CCD sensors with the colorimetric value obtained from the spectrophotometer. A correction equation for the colorimetric data of the CCD sensors is derived from the difference in the colorimetric data on the same patch measured by both sensors. This technology enables customers to obtain accurate colorimetric data over the entire area of the paper.
Category to which this technology applies
(click to see a list of technologies in that category)
\Our expert team handles inquiries
on technical partnerships and joint research./