1 INTRODUCTION
With increasing demands for safer and more secure society, the number of sensing and driver assistance cameras for auto mobile and surveillance camera in a city is rapidly increasing in recent years. Since they are mainly installed outdoors where the lens is exposed to severe environment of rain and polluted air, it is imperative for those lenses to ensure a clear view by keeping the surface clean and preventing a water droplet from forming on the surface. Therefore, super-hydrophobic property has attracted enormous attention and considered as an enabling technology in AR coating development in harsh environment. However, fabrication of these functions without compromising durability and an affordable price has been a great challenge in optical thin film design since etching process has been restricted to utilize expensive lithography technique, which limits the utilization of nano-structure to only the expensive devices.
2 FABRICATION OF HIERARCHICAL NANO-STRUCTURE FOR HYDROPHOBIC PROPERTY
A. Process flow
It has been well-known that lotus leaves exhibit super-hydrophobic property with its hierarchical rough surface of micro- and nano-structures consisting of convex cells and epicuticular wax crystals on top of the structure(Fig. 1) [1].
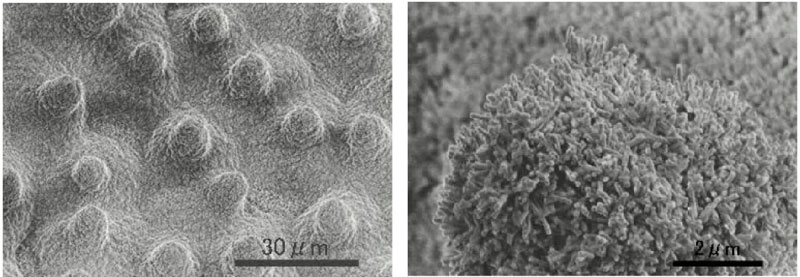
Fig.1 Hierarchical structure of lotus leaf
Hitachi High-Tech Corporation, accessed 19 March 2023, <https://www.hitachi-hightech.com/jp/ja/knowledge/microscopes/sem-tem-stem/microeye/05.html>
However, there has been two demanding challenges to apply these structure to commercially available lenses. One of the reasons is that it is difficult to artificially fabricate these micro- and nano-structure with a reasonable cost without compromising the abrasion resistance. Another reason is that the structure of these hierarchical rough structure needs to be modified in size down to about 200 nm at largest in order to avoid haze which degrades the transparency of lenses. For those reasons, a new process flow must be devised in a way that can simultaneously achieve a low cost, durable hierarchical rough surface, and controllability for size optimization. In this report, self-assembled Ag layer was applied on SiO2 layer as a mask fabrication process in order to easily form a well-controlled nano-pattern on a surfaces of lens without any lithography process (Fig. 2). Then, reactive CHF3 dry etching was adopted to engrave a rigid and durable nano-structures into the SiO2 layer. These processes were repeated twice so that hierarchical structure in different sizes were formed on the surface. Lastly, a hydrophobic fluoride material was deposited using evaporation deposition method which assumes a role of epicuticular wax crystals of lotus leaves.
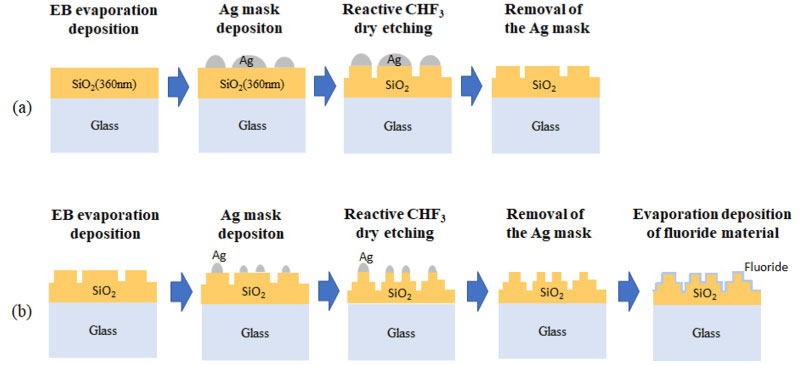
Fig. 2. Process flow of hierarchical nano-structure consisting of a) the first step and b) the second step
B. Self-assembled nano-mask-formation
The process needs to be applied on the curved surfaces of the lenses, however, it is particularly challenging for EB lithography as it is optimized for planar surface. Also, the mask formation process needs to be readily controllable so that the mask-pattern can be modified into preferably two different sizes to enhance the robustness of the structure. In addition, it is imperative to adjust the structure size below the wavelength of visible light to prevent light scattering from occurring. So, it is essential to identify these two mask-patterns to achieve both robust super-hydrophobicity and transparency of lens at the same time. Previously, several self-assembled masks were studied as a simplified nano-fabrication method [2-4]. In this report, simple Ag nano-mask was deposited using a conventional thermal evaporation technique optimizing the deposition rate, temperature of a substrate, and thickness of Ag layer to control the gap and pitch of Ag nano-mask(Fig.3).
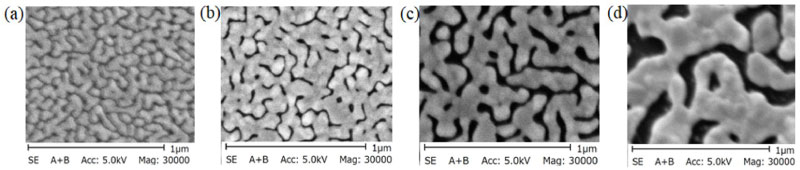
Fig. 3. SEM images of self-assembled Ag nano-structure mask at different depositing conditions.
a) Ag 14nm at 144°C, b) Ag 20nm at 150°C, c) Ag 20nm at 172°C, d) Ag 39nm at 300°C.
C. Etching process to engrave the nano-mask-pattern into SiO2 layer
After Ag nano-mask was optimized, the pattern was etched by CE-300I ICP-RIE (ULVAC) with CHF3 gas and the antenna/bias RF power of 400W/38W which provided etching rate of 0.9 nm/s for SiO2. Etching process insures the rigid and robust nano-structure since it is engraved the pattern into the previously deposited rigid SiO2 layer. Next, Ag mask was removed by aqueous potassium iodide solution of Pure Etch AU100 (HAYASHI PURE CHEMICAL). Fig. 4 shows the SEM image of etched SiO2 layer with optimized Ag nano-mask for the first step (a) and for the second step (b). As it can be seen in Fig.4 (b), area of convex parts for the second step is 49 %, which contributes the ability of repelling water droplet. And the average diameter of convex parts is 155nm, which is small enough to reduce Rayleigh scattering of light for optical devises..
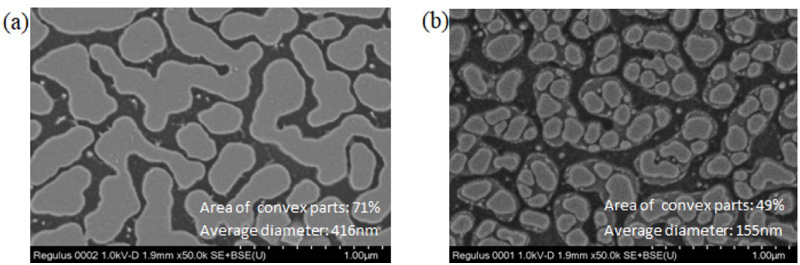
Fig. 4. Morphology of etched nano-structure of SiO2 layer after a) the first step, and after b) the second step.
Lastly, hydrophobic fluoride of UD120 (DAIKIN INDUSTRIES, LTD.) was deposited using thermal evaporation technique. This layer plays an equal role to epicuticular wax crystals on lotus leaves to enhance the hydrophobicity further.
3 APPLICATION TO OPTICAL LENS
Contact angle of water droplet of 10μl on the lens surface was compared in Fig.5 between normal hydrophobic coating and super-hydrophobic coating. While the normal hydrophobic coating has 115 degrees of contact angle, the super-hydrophobic coating shows 150 degrees in contact angle, which shows a excellent property of repelling water.
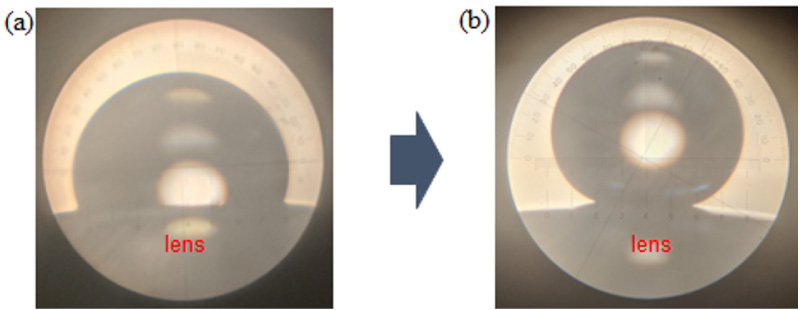
Fig. 5. Comparison of contact angle of water droplet on a lens surface
between a) 115°for normal hydrophobic coating and b) Super-hydrophobic coating.
A video of Fig.6 shows a behavior of water droplet on a lens surface with super-hydrophobic coating. Water droplet is easily rolls off the surface due to the lotus effect of micro- and nano-structures and fluoride coating on top of it. Also, the video indicates that there is no undesired diffraction pattern of light due to the random pattern of the nano-structure, which is hard to achieve with lithography process. At the same time, light scattering is well suppressed to enhance transparency owing to the optimized size of nano-structure below the wavelength of visible light.
Fig.6 Video of water droplet rolling off the super-hydrophobic surface.
Optical lens for any camera generally requires an anti-reflection property to prevent lens flare or lens ghost using multi-layer coating technique. In this report, moth-eye anti-reflection technique instead of multi-coating technique was used to suppress the reflection. As it can be seen in Fig.7, the reflectance is controlled below 1 % in the entire range of visible light from 400 nm to 750 nm.
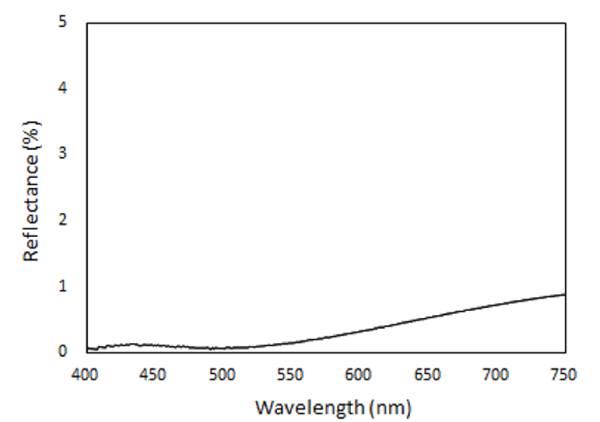
Fig. 7. Reflectance of a lens with super-hydrophobic coating.
4 DURABILITY TESTS OF SUPER-HYDROPHOBIC COATING
In order to apply the coating to comercially avialable camera, it is also crucail to maintain the initial peformance over time. Since cameras are susceptible to different climate conditisons various environmental tests needs to be performed to fit the coating to use in commerical devices. Fig.8 shows the result of accelerated environmental tests. As can be seen, the coating retained excellent performance of above 145 degrees over 1,000 hours in contact angle against most tests. Although only sunshine tests degraded the contact angle down to 138 degrees over time, it is still above the critical point of 130 degrees where water droplet stops rolling off the lens surface.
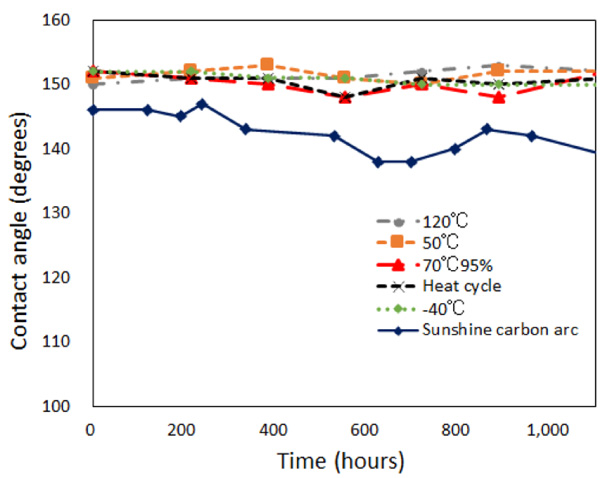
Fig. 8. Changes of contact angle over time against various environmental tests
Apart from environmental tests above, a scratch test was conducted to assure the robust features of the hierarchical nano-structure as shown in the following video.
Fig. 9. Abrasion test for coating with load of 250g/cm2.
Since coatings for commercial cameras get affected by external forces such as collision and scratches, the super-hydrophobic coating needs to be highly resistant to any sort of conditions or scratches. In this report, the coating was intact after 2,000 reciprocating scratches test with load of 250g/cm2 due to the optimized hierarchical nano-structure.
5 CONCLUSION
Durable super-hydrophobic antireflection coating with hierarchical nano-structure was successfully demonstrated. First, the fabrication process of durable hierarchical nano-structure imitating lotus leaves was introduced along with the self-assembled Ag nano-mask fabrication process which is suitable for a curved surface of lenses and for a mass production. Then, the performance of super-hydrophobicity was shown in a video using actual lens with the coating. Lastly, the durability of the super-hydrophobic performance was evaluated through the environmental tests and abrasion test, which proved the reliable performance of super-hydrophobicity over time.
Acknowledgement
This research was supported by VLSI Design and Education Center (VDEC, now Systems Design Lab, School of Engineering), The University of Tokyo in Japan as well as “Nanotechnology Platform Japan” of the Ministry of Education, Culture, Sports, Science and Technology (MEXT) Grant Number JPMXP09F18UT0047. We would like to express our sincere gratitude to them and to people in UTokyo Mita lab for not only sharing well maintained EB lithography, dry etching, and SEM machine but also sharing their expertise and experience in the field of microfabrication.