1 はじめに
コニカミノルタではこれまで、ディスプレイ市場向けにセルロース系の材料(TAC1、変性TAC樹脂)による偏光板保護膜および光学補償膜の光学フィルム事業を展開してきた。市場ニーズや市場変化を先読みし、コア技術である溶液製膜技術、添加剤技術をベースに顧客へ価値提供を続けてきた。
顧客ニーズの多様化により、ディスプレイの反射防止能やUVカット能、高耐久性と達成すべき機能が高次化している。折り畳み型スマートフォン、超薄膜スマートフォン等へと利用領域が拡大していく中で、TACに加えて新材料を用いた新世代SANUQI(サヌキ)、新世代アクリルSAZMA(サツマ)2)と様々なタイプの樹脂を取り扱うプロセスへ転換を進めることで顧客ニーズに継続的に応えてきている。
2 光学フィルムの製膜方法
光学用の高分子フィルムの製膜方法は溶融製膜法、溶液製膜法に分類される(Fig.1)。溶融製膜法は熱を加えて原材料であるポリマーを融かすことで、溶液製膜法は溶媒を用いることで、原材料に流動性を与え、流体を膜になるように押し出して製膜する方法である。溶融製膜法はポリマーを熱で融かすため、分子量が大きい高分子材料や熱に弱い添加剤を扱うことができないのに対し、溶液流延法は溶媒を用いて溶かすことで、熱に弱い添加剤も含めて幅広い添加剤の選択が可能である。
また、溶液製膜法は、ドラム方式とベルト方式に分類される。ベルト方式は流延後の乾燥時間制御が容易であり、薄膜製膜に対しても有効である。
コニカミノルタでは溶液製膜法とベルト方式を採用している。高分子量ポリマーと各種添加剤を加えて溶媒を用いて溶解した後、支持体であるバンドベルト上に流延し、ある程度溶剤が揮発した後、自己支持性をもったところで剥離し乾燥・延伸工程を経て製品フィルムを得ている。連続生産されたフィルムは円筒状の巻き芯に巻き取られ梱包することで製品形態となる。
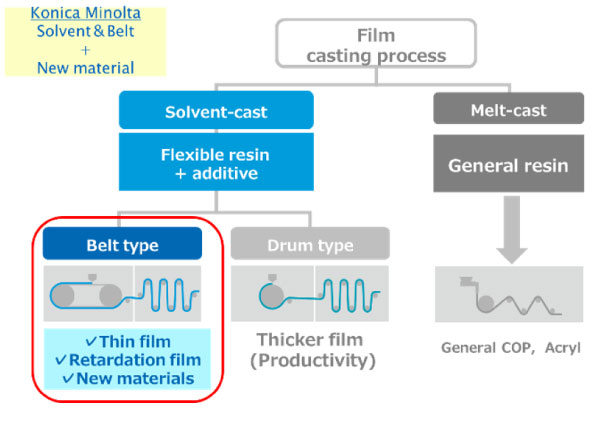
Fig. 1 Three different casting processes.
Methods of manufacturing polymer films fall into two types: solution casting and melt casting. In solution casting、 either a drum type or a band belt type of support is used. We use a band belt support because its wide range of film thicknesses allows easy control of the long drying process following casting.
3 SANUQIの製品展開
3. 1 SANUQIの特徴 2)
SANUQIは、シクロオレフィンポリマー(COP)の一種を製膜したフィルムで、耐水性・耐熱性・透明性に優れた特性を有しており、特に溶液製膜法との親和性を高めるために通常より高分子量に調整した。結果、靭性を付与することができ従来の溶融製膜法による耐水性フィルムでは達成し難い製品の薄膜化・広幅化・長尺化の要望に応えられるようになった。SANUQIの材料特性と機能を生かした商品群領域をFig. 2 に示す。
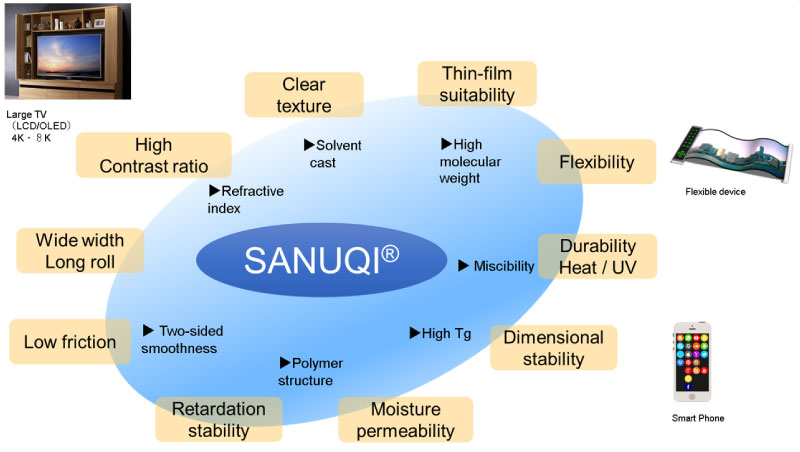
Fig.2 Characteristics and functions of SANUQI film.
The figure shows the characteristics and functions of SANUQI with suitable applications
4 製品拡大を支えるDX
4. 1 フィルム生産現場でのDX(digital transformation)の必要性
前章でも述べたようにコニカミノルタでは、これまで溶液製膜法を用いて高品質なTACフィルムを安定的に提供してきた。しかし、TACに加えて新材料を用いた製品展開を進める中で、新材料では熱等の外部要因の影響がTACに比べて大きく、生産トラブルの増加を招いている。また、知見者の退職などの人的要因によるナレッジの継承も課題となっている。
これらを改善するために、フィルム製造での監視や判断に用いているカン・コツ・経験からの脱却をDXの定義と置き、この施策の1つとして画像処理を活用したシステムを開発した。
4. 2 主な生産トラブル
光学フィルムの製造は連続生産方式であり、自動車生産などで用いられる組み立て生産方式とは異なる。上流から下流までの複数工程が連続的に行われる化学プラントのイメージに近く、一度トラブルが発生すると他プロセスに影響を及ぼし、かなりの工程遅延や復旧工数が必要となる。
特に光学フィルムは数十ミクロンの薄膜であるため、搬送条件によっては搬送フィルムにフラッタ(ここではフィルムのバタつきを示す)が発生し易く、生産難易度が高い。フラッタによるトラブルは温度、張力、風量など様々なプロセス要素のかけ合わせで発生する。そのため、定量化ができない事象も多く、本質改善に時間がかかることもあった。
4. 3 画像処理システムの概要
先の記述の通り、フラッタによるトラブルは複数の要素のかけ合わせで発生することに起因するため、人の目による官能的な監視が行われている。情報の塊であるフラッタを定量的に扱うことが本質解決に繋がると考えている。
この官能的な情報を有効活用すべく、コニカミノルタのコア技術である「画像処理」を用いて、フィルム製造特化した監視の定量化・自動化を行う画像処理システムを考案した。(Fig.3) このシステムは”現場で使える”ことをコンセプトとして設計を行っている。これは一般的な画像処理ソフト等と異なり、フィルム製造での頻発する生産トラブルを元に選定された3種のアルゴリズム(輪郭抽出、フレーム間差分、距離計測)に機能を絞ることで複雑化を避けつつ汎用性を高めることと、直感的に利活用可能なGUIを搭載することで実現している。
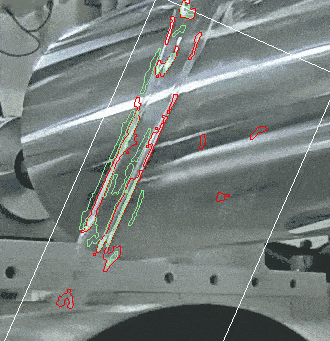
Fig.3 Real-time image processing system operation screen of film(Red:Strong flutter areas、Green:weak flutter areas)
このような画像処理システムを用いることで現場の知見者が持っていた監視のノウハウや感覚を定量的なデータとして保存・共有が可能となるだけでなく、これまで人の目ではわからなかった微細な変化にも対応できるようになった。また、定量的なデータとなった事で、データサイエンスの変数としても用いることができるため、官能的な評価しかできていなかった部分も網羅したデータ解析が可能となった。これにより、異常傾向への気づきやトレンド同士の結びつきを紐解くことができ、トレンド監視システムなどと組み合わせた客観的な判断を行うことで生産トラブルの低減に繋がっている。
4.4 導入実績と効果
4.4.1 フラッタの定量化
フラッタによる生産トラブルでの活用事例を紹介する。
フラッタは大きくなりすぎると、それがきっかけとなり、生産トラブルを引き起こす。しかし、これまで人の目で監視を行っていたため、この変化に気づくのが遅れて生産トラブルを防げないことがあった。
一方、画像処理システムを用いてフラッタを定量化した(Fig.4)ところ、フラッタがトラブルの数時間前から徐々に変化し、生産トラブルを招いていることが判明した。フラッタが変化し始めた段階で適切な処置を行うことができればトラブルを防ぐことが可能となる。
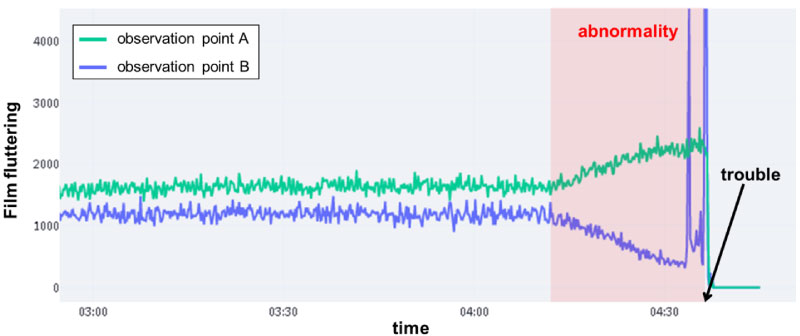
Fig.4 Flutter Quantification Trends(Green: observation point A ,Blue: observation point B)
また、発生したトラブルの原因解析においてはこの変化点を異常と正常の境目の情報とすることで、機械学習を用いた関連トレンドのピックアップを行っている。そこで得られた結果に対して対処を行うことで生産トラブルの根本解決に繋がる。
4.4.2 その他の事例
フラッタ以外のトラブルに対しても画像処理システムを用いた状態監視や定量化が進んでいる。この1例として熱溶着プロセスの出来栄え評価での使用例を示す(Fig.5) 。図中の赤色で示されたフィルム端部の実線とこのデータから得られた近似線との距離を測定することでトラブル発生の危険度を図ることができる。
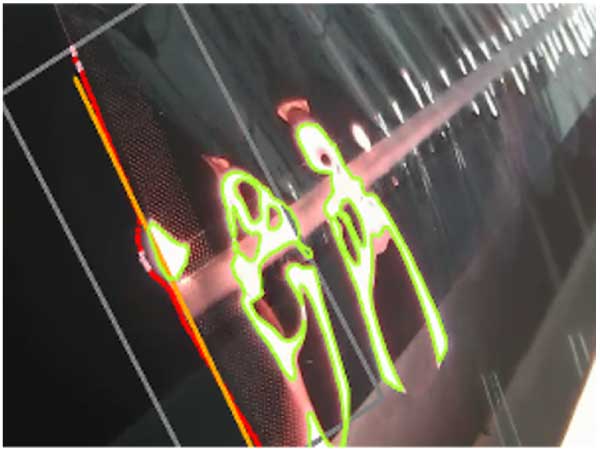
Fig.5 Quantification of film joints(Red: Solid line at film edge、Orange: proximal line)
4.5 さらなるスマート工場化に向けて
生産トラブルの増加やナレッジの形骸化を本質的に改善するためにはDX(デジタルトランスフォーメーション)を用いた様々なナレッジの蓄積とこれを用いた判断、対応の自動化が必要と考えている。過去に繰り返し発生したトラブルに対し人の介在しない自動対応システムを活用すれば、担当者の工数を新規トラブルや原因解析に捻出でき、より本質的な改善に繋がると考える。
本稿で紹介した画像処理システムもこの構想の一部であり、全体像はFig.6に示すような様々なシステム群との連携で実現する計画である。
工場から抽出されるデータに対し、過去の生産トラブル情報や異常検知アルゴリズムをもとにリアルタイム監視を行い、トラブルが発生する前に対応を行う。それでも発生する生産トラブルについてはデータサイエンス等を用いた原因調査を行い、トラブル事例としてシステム内に組み込むことで次回以降は自動的にFB制御がかかる仕組みになっている。
このようなサイクル(Fig.6)を回すことで自動的にナレッジが蓄積する状態を作ることができ、同時に誰でも閲覧可能な情報として共有が可能である。現在、このシステム開発に向けた取り組みを加速している。
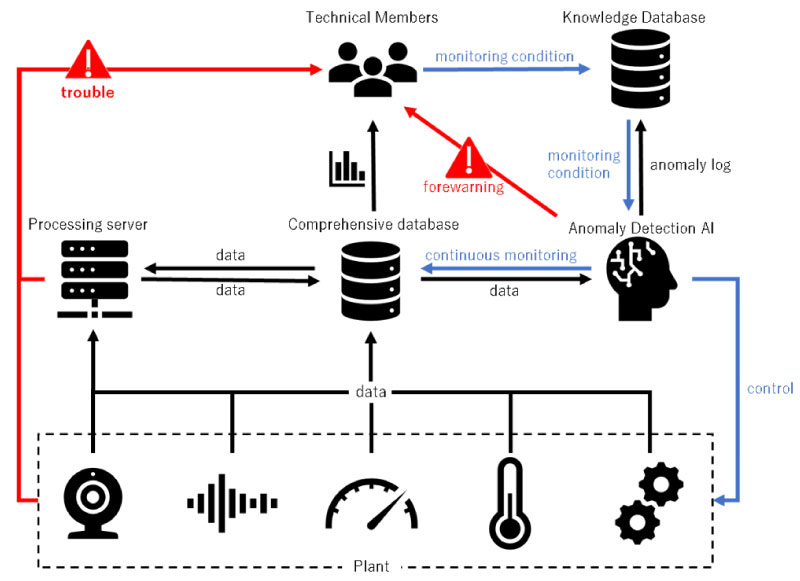
Fig.6 Conceptual diagram of system linkage
一方で今回の報告のようなフィルムの生産トラブルは我々の顧客を含む一般的なフィルム産業でも同様に発生していることが考えられる。しかし、一般的な画像処理ソフトでは機能がマッチしない等の理由で導入難易度が高いことが多い。そのため、これに特化した画像処理機能をコニカミノルタの画像IoTプラットフォーム「FORXAI」等と連携し、新たな商品として提供することで顧客生産性の向上にもつなげていきたいと考えている。