1
Overview
Konica Minolta has been promoting automation to continuously reduce the cost and improve the manufacturing quality while coping with challenges in the manufacturing industry, such as the difficulty of securing human resources and the surging labor cost. The Business Technologies Business has been promoting automation using dedicated equipment mainly for large-lot products, namely, consumables for multi-functional peripherals (MFPs) for offices. In recent years, the division has been expanding the scope of automation to consumables for production print machines. Because the production volume of production print machines is smaller than that of MFPs, the use of dedicated systems as in the case of conventional systems results in a low return on investment. Thus, the scope of automation was limited to some processes, such as the inspection process for ensuring quality. This report introduces an initiative in which we reduced the installation space by 50% compared to that of conventional dedicated systems, built an automation line for mixed-model manufacturing (Fig. 1) with capital expenditure reduced to 60%, and realized efficient manufacturing based on high-quality, low-cost automation through the new combination of advancement in automatic assembly technology with a product design that assumes automatic assembly.
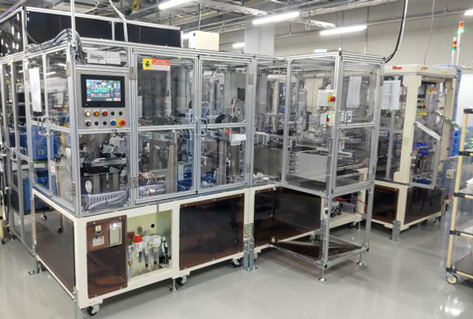
Fig. 1 Automation line for mixed-model manufacturing
2
Details
■Configuration
Charging corona units are consumables for Mid Production Printers (MPPs) and Light Production Printers (LPPs). Due to the performance difference, the product structure of charging corona units for MPPs is different from that for LPPs.
In addition, MPPs and LPPs are designed assuming manual assembly because the functionality is high and the structure is complex compared to MFPs. It was difficult to achieve automation using conventional technologies.
Against this backdrop, we reviewed the conventional concept of dedicated equipment from scratch, and pursued two approaches: advancement of automatic assembly technology and a product design reflecting the requirements suitable for automation. We realized automatic assembly by mixed-model manufacturing of two different products.
■Functions / Features / Applications
1. Advancement of automatic assembly technology — release liner removal technology for soft material seals
Seals of different materials and sizes are used in information devices for sealing and cleaning. To remove the release liner of label seals using automatic equipment, a commonly used technology is to cut and separate seals from the release liner by using the rigidity of the material and folding the release liner in an acute angle. However, seals used for charging corona units are made from a thin moquette material that is not rigid with a thickness of only 1 mm. The seals are also very small, measuring only 4 mm by 4 mm. Thus, it was difficult to stably remove the release liner using conventional technology.
Thus, we used a new system to pinch with the upper and lower claws. As shown in Fig. 2, 1) the lower claw, whose edge is very thin and sharp, is slightly inserted between the adhesive surface of the seal and the release liner in the horizontal direction. Then, 2) both the moquette and the base material are reliably pinched from the oblique direction using the upper claw and are removed upward in the oblique direction. This technology enables the release liner to be removed from soft material seals.
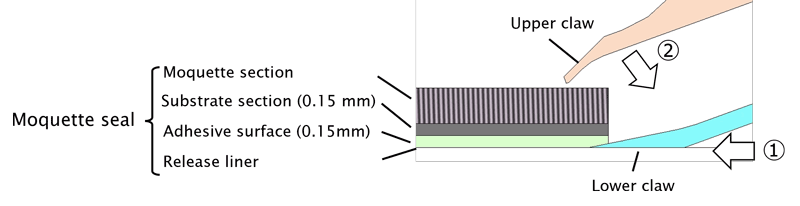
Fig. 2 Schematic diagram of release liner removal technology
2. Product design reflecting the requirements suitable for automation
2-1. Standardization of the process
In mixed-model manufacturing where products with different structures are manufactured, it is essential to standardize the assembly process for different products in order to reduce the system cost. To realize this, we also designed a concept for automatic equipment from the product design phase.
The assembly process for a component called a “cover” is described as an example. As shown in Fig.3, in the design before modification, the clamping function for preventing the cover from coming off was provided only for MPPs. This difference made it difficult to standardize the assembly processes for the two models. To solve this issue, the structure was modified to clamp the cover with the snap fit shape. The design enabled assembly in the downstream process, thus standardizing the process.
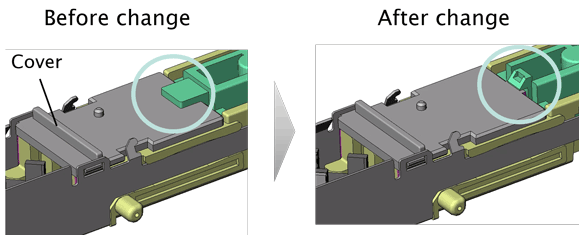
Fig. 3 Example of a design for process standardization
2-2. Part shape that facilitates recognition and identification of object images
In mixed-model manufacturing, a parts feed system must be installed depending on the number of models manufactured, which increases the required space. Against this backdrop, we aimed to reduce the footprint and cost of parts feed systems by combining image recognition with robots. However, in conventional technology, it was necessary to introduce an expensive image recognition system to stably identify the orientation of parts whose contour edge shape on the front is similar to that on the back.
Thus, as shown in Fig. 4, we modified the parts design and added characteristic ribs to increase notches and internal edges. In addition, images were captured under different conditions to perform image processing to emphasize the differences in the internal characteristics. We established an image recognition system by combining the internal edge identification algorithm for identification based on the internal edge information with the contour edge identification algorithm for identification based on the external shape characteristics of parts.1)
Accordingly, we developed an object image recognition system, as shown in Fig. 5, using an inexpensive 2D camera at a system cost less than one fifth of that of commercially available products, reducing both the footprint and cost of parts feed systems.
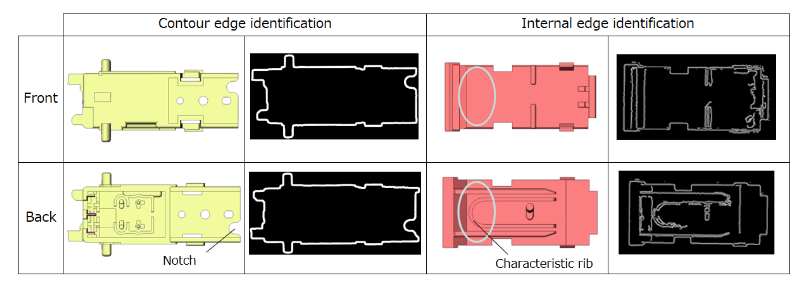
Fig. 4 Example of image assessment
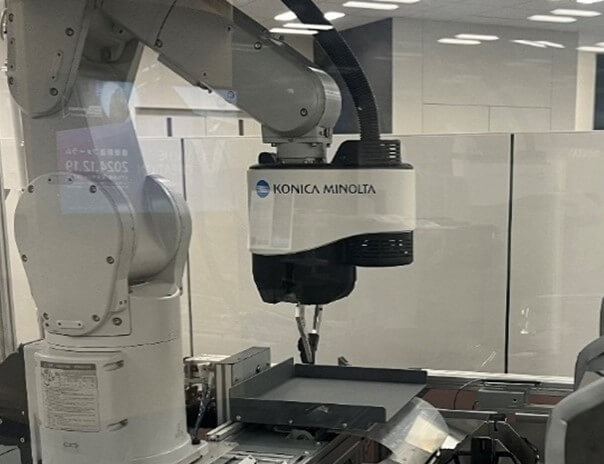
Fig. 5 Image recognition system
■Future outlook
We worked on both the advancement of automatic assembly technology and a product design suitable for automation. We introduced an automation line for mixed-model manufacturing even for products with a small production volume and realized space-saving and low-cost automation.
In addition, we will establish the requirements suitable for automation as design standards and apply them from the upstream process of product design to expand the scope of automation and promote manufacturing innovation.