1 概要
コニカミノルタでは、モノづくりを取り巻く環境である人材確保の困難さ、人件費の高騰といった課題に対応しつつ、継続的に原価低減と製造品質の向上を図るため自動化を推進している。情報機器事業部では、これまでオフィス向け複合機(multi-functional peripherals, MFP)向け消耗品である大ロット製品を中心に専用機による自動化を進めてきたが、近年、プロダクションプリント向け消耗品への自動化の適用拡大に取り組んでいる。プロダクションプリントはMFPと比較すると生産数が少ないため、従来と同じ専用装置では投資採算性が合わず、品質を担保するための検査工程への導入など一部の工程の自動化に留まっていた。本報では、新たに自動組立技術の高度化と自動組立を前提とした製品設計を融合させることで、従来の専用装置と比較し設置スペースを50%削減し、設備投資を60%に抑えた機種混流自動化ライン(Fig. 1)を構築し、高品質かつ低コストな自動化による効率的なモノづくりを実現した取組みを紹介する。
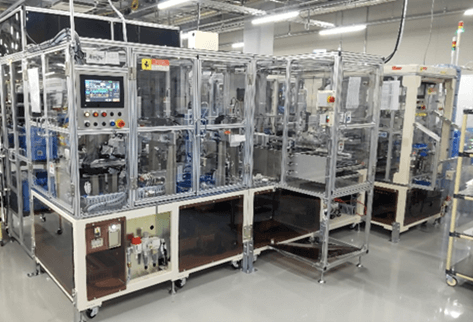
Fig. 1 機種混流自動化ライン
2 詳細
■構成
中速プロダクションプリンター(Mid Production Printer, MPP)と低速プロダクションプリンター(Light Production Printer, LPP)のそれぞれに搭載される消耗品である帯電極は、性能の違いから異なる製品構成となっている。さらにMFPに比べて高機能で複雑な構成のため、手組を前提とした製品設計となっており、従来技術では自動化は困難であった。そこで従来の専用装置の考え方を一から見直し、自動組立技術の高度化と自動化に適した要件を反映した製品設計の2つのアプローチで取り組むことで異なる2つの製品の機種混流生産による自動組立を実現した。
■機能/特長/用途
1. 自動組立技術の高度化-軟素材シールの剥離技術
情報機器では、封止や清掃などのため素材や大きさなど多種多様なシールが使用されている。また、自動機によるラベルシールの剥離作業は、素材の剛性を利用し、剥離紙を鋭角に折り返すことでシールと剥離紙を切り離す技術が用いられるのが一般的である。しかし、帯電極に使用されるシールは、厚さがわずか1 mmと薄く剛性のないモケット素材で、サイズも4 mm四方と非常に小さいため、従来技術では安定して剥離紙を剥がすことが困難であった。
そこで、新たに上下の爪で挟む方式を採用し、Fig. 2に示すように①極薄で鋭角な先端形状を持つ下爪をシール粘着面と剥離紙の間に水平方向にわずかに侵入させ、次に②上爪で斜め方向からモケット部だけでなく、基材部も確実に挟み込みながら斜め上方へ引き剥がす技術を確立し、軟素材シールの剥離を可能にした。
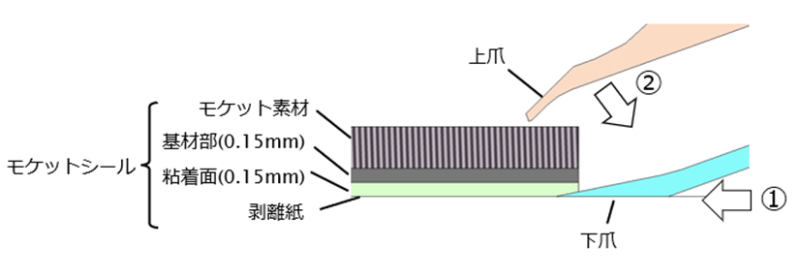
Fig. 2 シール剥離技術模式図
2. 自動化に適した要件を反映した製品設計
2-1. 工程の共通化
構成が異なる製品を生産する機種混流生産においては、製品間で組立工程を共通化することが、装置コスト抑制の観点において重要である。これを実現するため、製品の設計段階から自動機も並行して構想設計を進めた。
一例として、カバーと呼ばれる部品の組立工程を挙げる。Fig. 3のように、変更前の設計では、MPPのみにカバー脱落防止のための抑え込み機能が存在しており、この差異により、2機種間で組立工程を統一することができなかった。この課題を解決するため、変更後のようにカバーをスナップフィット形状で抑え込む構成とすることで後工程での組立が可能な設計とし、工程の共通化を実現した。
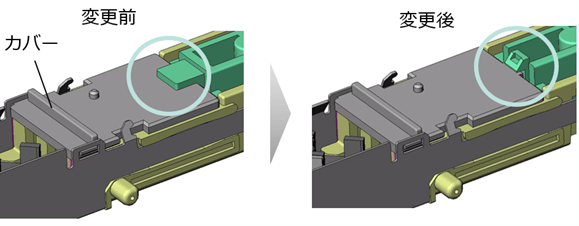
Fig. 3 工程統一のための設計事例
2-2. 物体画像認識と判別を容易にする部品形状
機種混流生産では、生産機種数に応じて部品供給装置を設置するため必要スペースが増加する。そのため、画像認識とロボットの組み合わせによる部品供給装置の省スペース化と低コスト化を目指したが、従来技術では表裏の輪郭エッジ形状が類似する部品の姿勢を安定して判別させるためには高価な画像認識システムを導入する必要があった。
そこで、Fig. 4に示すように部品の設計を変更し、切り欠きや内部エッジを増加させる特徴リブを追加した。さらに複数の条件下での撮像を行い内部特徴差を強調する画像処理を施し、内部エッジ情報に基づいて判別する「内部エッジ判別アルゴリズム」と、部品外形の特徴に基づいて判別する「輪郭エッジ判別アルゴリズム」を組み合わせた画像認識システムを構築した。1)これにより、安価な2Dカメラを用いて市販品の1/5以下という装置コストでFig. 5に示す物体画像認識システムを開発し、部品供給装置の省スペース化と低コスト化を実現した。
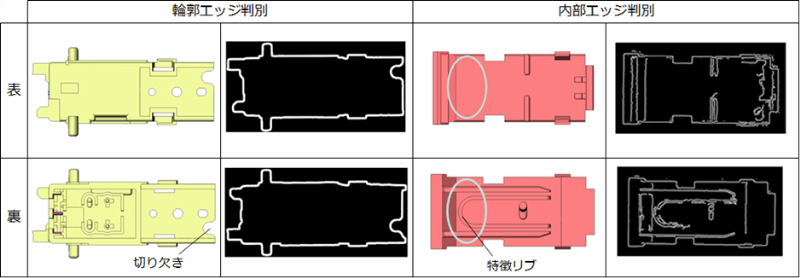
Fig. 4 画像判定事例
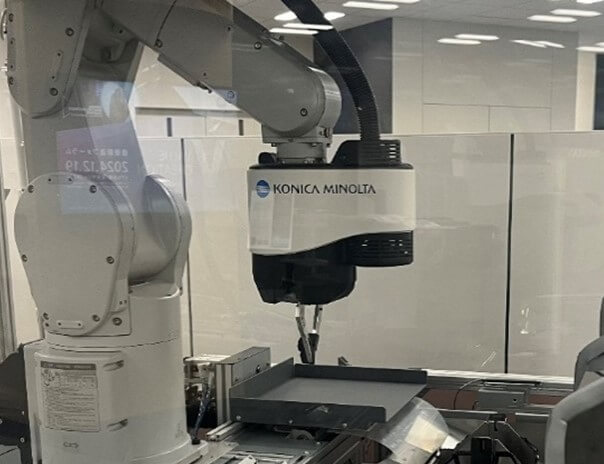
Fig. 5 画像認識システム
■今後の展望
自動組立技術の高度化と自動化に適した製品設計の両輪で取り組むことで、生産数量の少ない製品に対しても機種混流自動化ラインを導入し、省スペースで低コストな自動化を実現した。さらに自動化に適した要件は設計標準として蓄積し、今後の製品設計の上流から適用を進めることで自動化領域の拡大を図り、モノづくり革新を推進していく所存である。