Material design technology for functional toner
Designing toner with low environmental impact by saving energy with low-temperature fixing performance and using plant-derived substances
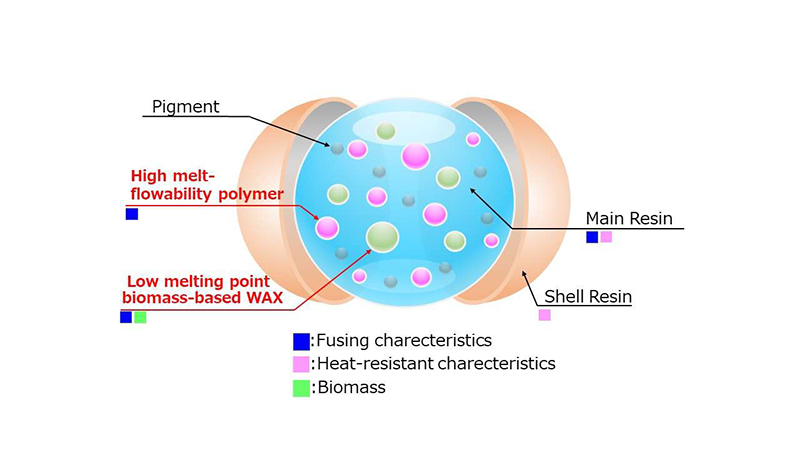
New chemical toner that helps customers save energy and improve productivity
To help create a sustainable society, Konica Minolta is committed to developing chemical toner that consists mainly of a styrene-acrylic resin using a radical reaction with low energy during manufacture, and adopts an emulsion polymerization and agglomeration method.
After 2001, when our first-generation chemical toner was released, Konica Minolta started developing a toner that could be fixed at a lower temperature, and succeeded in developing a 5th generation chemical toner “Simitri V Toner,” which it released in 2019.
We reduced the fixing temperature by about 15°C from the previous toner, enabling our customers to reduce annual CO2 emissions from printing by about 20 to 25%. The lower fixing temperature also increased printing speed; Konica Minolta’s digital printing machines offer the industry-leading printing speed of 140 sheets a minute and improve customers’ productivity.
Technology Overview
Toner needs to achieve two opposing functions – heat resistance and low temperature fixing. Konica Minolta has developed the latest “Simitri V Toner” utilizing the following two technologies.
One is a technology for modifying the resin structure to optimize the state of the main resin and the functional resin. The other technology is a structural control technology using phase inversion emulsification, which is a chemical emulsification method that reduces the energy consumed during manufacture.
These technologies have made it possible to control the compatibility/incompatibility between the main resin and the functional polymer, realizing both satisfactory heat resistance due to incompatibility at ordinary temperature and satisfactory low temperature fixing due to considerably reducing the melting viscosity by compatibilization during fixing. In addition, the core-shell high-order structure separates functions by uniformly dispersing the material in the toner and forming a shell layer. Moreover, we have succeeded in realizing both low-temperature fixing and lower environmental burden by using a plant-derived wax that melts at a low temperature.
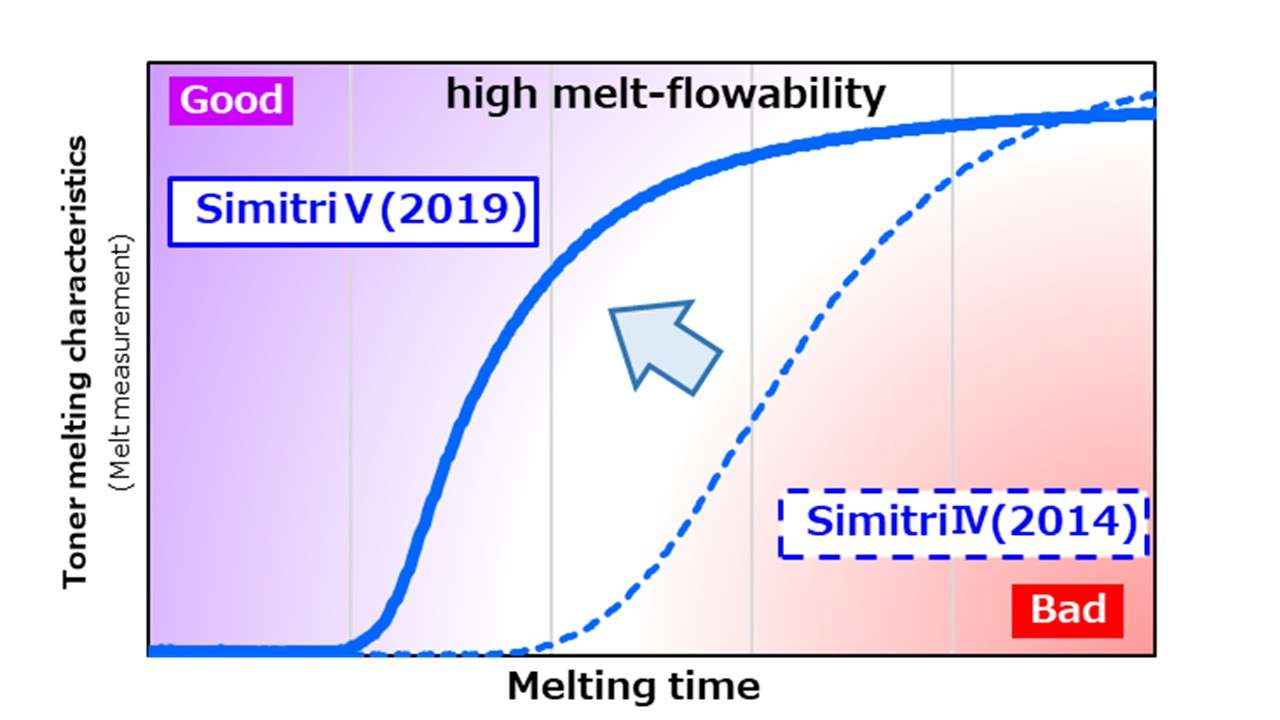
Comparison of melting characteristics between 5th and 4th generation toners
Toner manufacturing process that flexibly places components
Konica Minolta adopts an emulsion polymerization and agglomeration method to manufacture toner. This method builds up toner by producing and agglomerating fine resin particles of submicron size or smaller. In the future, this manufacturing process will enable the control of the dispersed state of the material in the toner, core-shell design, and the introduction of a wide variety of materials and diverse performance capabilities.
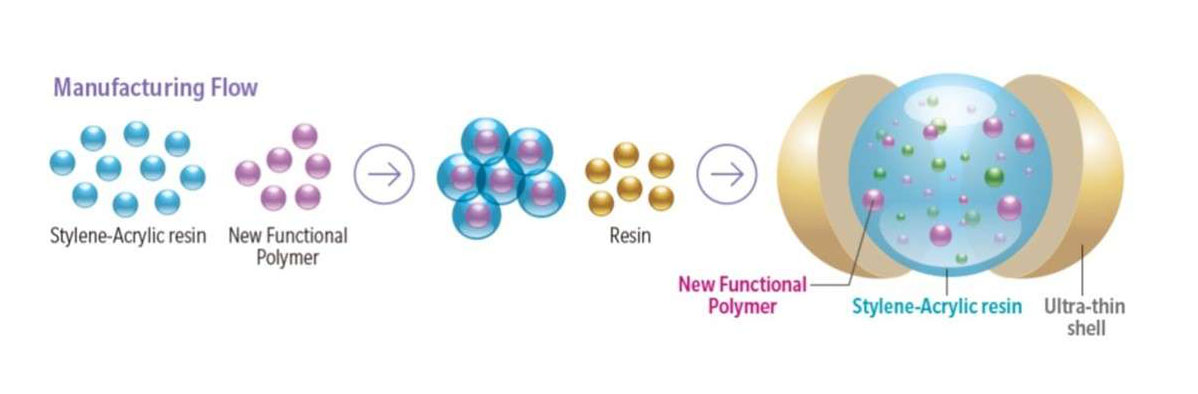
Category to which this technology applies
(click to see a list of technologies in that category)
\Our expert team handles inquiries
on technical partnerships and joint research./