1 はじめに
当社のデジタルカラー印刷機では色ずれ品質向上のため感光体ドラムと中間転写ベルトなどの画像形成部におけるモーター駆動を高精度に制御する技術(精密駆動技術)が採用されている。ラベル・パッケージ印刷に代表されるロール紙に対応したデジタルラベル・パッケージ印刷機AccurioLabel 400(以下、AL400とする)において、精密駆動技術に加え、ロール紙走行速度制御、自動品質最適化ユニットIQ-501をロール紙向けにアップデートしたIQ-520でのリアルタイム画像位置検出、及び、画像処理による制御を新たに採用し、長距離連続印刷において安定した画像品質を実現したので報告する。
2 色ずれについて
色ずれとはカラー画像におけるYMCBk+White各色トナー像の位置ずれを示し、相対位置が一致しないことにより画像品質を劣化させる。色ずれには露光デバイスの静電潜像書き込み方向である主走査方向のずれと、通紙方向の副走査ずれがある。
近年、デジタルカラー印刷機の高速化が進み、用紙搬送による画像形成部への変動影響が顕著となり、通紙方向の副走査方向のずれが問題となっている。
副走査方向のずれの成因をFig. 1にて説明する。色ずれの主要因として、メカニカルな部品精度、用紙から受ける変動、また、機械内部の温度上昇を起因とする画像形成部材の膨張収縮などがあり、中間転写ベルト(Transfer belt)などの画像形成部品の位置変化や、駆動部の瞬間的な速度変動で発生することがわかっている。その中でも、ダイナミックに動作する用紙搬送の影響について記載する。
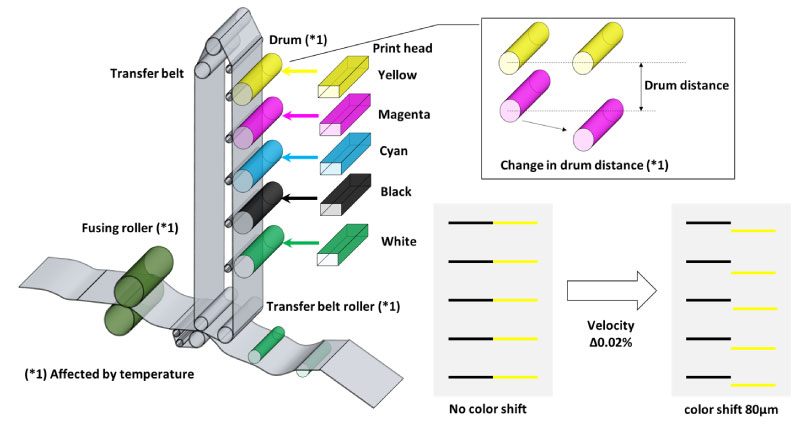
Fig. 1 Color shift due to rotational speed difference between drums.
2.1 デジタルカラー印刷機
枚葉機(1枚ずつカットされた紙を印刷機に通す方式)では、用紙が一定の間隔で走行していることから、副走査方向の色ずれ補正に優位な点として以下の3点があげられる。
1点目は、中間転写ベルトが2次転写部を通して用紙から受ける力が連続的とならず、精密駆動技術で中間転写ベルトの速度変動抑制が可能である。
2点目は1点目とは逆に、用紙間隔が空くことから、2次転写部の用紙突入による変動が用紙ごとに発生し、瞬間的な副走査方向のずれを引き起こすが、精密駆動技術により瞬間的な変動を抑制することが可能である。
3点目はプリントの途中にJOBを停止させて、機械内部の温度や画像形成部品の状態変化に応じた色ずれ補正の実施が可能である。
2.2 デジタルラベル印刷機
ロール紙が連続的に中間転写ベルトに与える変動について、Fig. 2で説明する。ロール紙は給紙部であるワインダーから一定テンションを維持された状態で2次転写部に搬送され、1次転写、2次転写を経たトナー定着後にロール紙巻き取り部であるリワインダーにて巻き取られる。
色ずれの成因で述べた通り、画像品質の維持にはロール紙を安定的に走行させることが必要となる。そこで、我々はその手段として定着ローラーを選択した。定着ローラーは機械下流に位置し、ロール紙に安定したテンションを与え、かつ、強いニップ力により走行性を確保するのに最適であると考えたからである。しかし、定着ローラーは、温度の影響を強く受けて熱膨張が起こるだけでなく、ニップ力が高いためローラー偏芯による周速度の変化が発生することが分かっている。
ロール紙特有の副走査方向のずれは、この定着ローラーの周速度変化がロール紙を通して連続的に中間転写ベルトに伝わり、定着ローラーに同期して中間転写ベルトが引っ張られたり押されたりすることで発生する。このロール紙から受ける連続的に作用する変動を感光体駆動や中間転写ベルトの精密駆動技術のみで抑制することは困難である。
また、枚葉機の3点目に挙げた特徴に対して、デジタルラベル印刷機は連続プリント中に色ずれ補正を行うと画像間隔が空いてしまい、断裁時の後加工処理に影響を与えるため、連続プリント中の色ずれ補正の適用ができないシステムである。よって、安定した画像品質を維持するためにはデジタルラベル印刷機特有の補正手段が求められる。
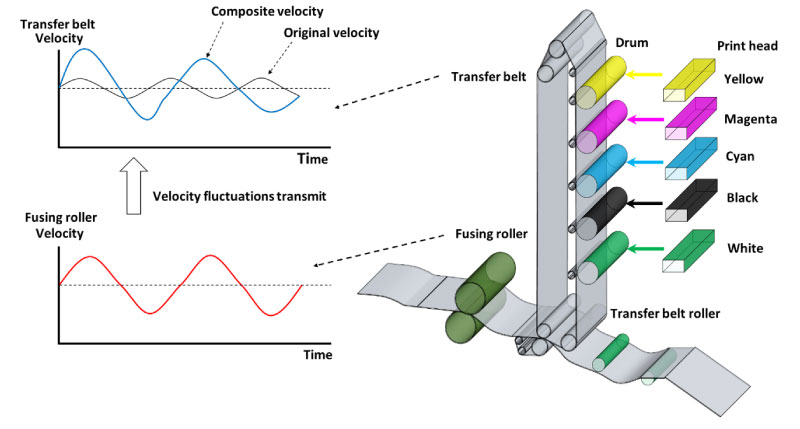
Fig. 2 Transmission to intermediate transfer belt speed fluctuation.
3 採用技術
ロール紙による副走査方向のずれを低減、および、補正する技術について説明する。
色ずれの成因にあるように、ロール紙の走行速度に影響を及ぼす変動要因を回避するための用紙速度制御と、画像形成部の熱膨張で発生する色ずれをリアルタイムに検知し補正するリアルタイム色ずれ補正の2つの技術を採用した。
1)用紙速度制御
ロール紙の走行性を決める定着ローラーの偏芯成分や熱膨張による周速度変化を精度よく検知し補正するために、定着ローラー1回転の変動成分を独自のフィルタリング技術を採用することとした。抽出された定着ローラー1回転の変動成分に対して、演算処理を経て定着ローラー駆動モーターの速度を制御することで、副走査方向のずれを低減する。
2)リアルタイム色ずれ補正
ロール紙端部に描画された色ずれ検出用パッチを本体後段のIQ-520でリアルタイムに読み取り、色間の副走査方向のずれ量を算出し、画像データ平行移動量にフィードバックすることでプリント初期からの経時的な副走査方向のずれを低減する。
4 用紙速度制御
4.1 システム構成
AL400の画像形成システムをFig. 3に示す。ロール紙搬送経路(赤線)上に設けられた用紙速度を検出する検知ローラーと用紙を搬送する定着ローラー、及び、YMCBk+Whiteの画像形成を行う中間転写ベルトから構成されている。
検知ローラーの軸にはスリットを所定間隔で設けた円形状部材と用紙速度を算出するためエンコーダーセンサーで構成され、用紙が搬送されることで検知ローラーが回転しパルス信号を出力する。また、エンコーダーセンサーはエンコーダホイールの偏芯成分を除去するため180度の位置に対向するよう配置している。
エンコーダーセンサーからのパルス信号は制御基板に入力され、所定時間内に入力されたパルス数から用紙速度を算出する。この算出結果を用いて、4.2項で示す定着ローラー駆動モーターの速度制御を行い、用紙速度を一定に維持している。
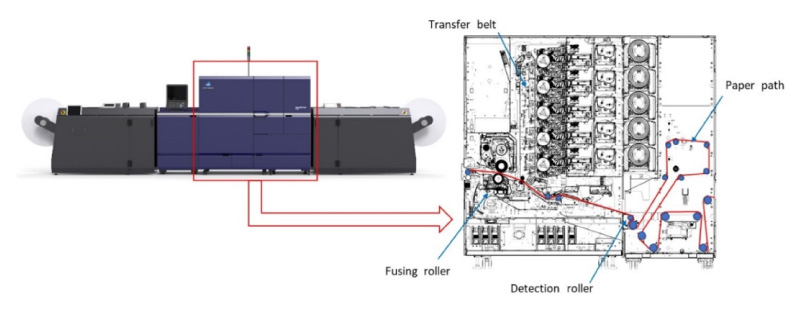
Fig. 3 AL400 Image forming system.
4.2 用紙速度制御の詳細
Fig. 4にて用紙速度制御の構成について示す。この用紙速度制御は2つの制御ループで構成している。
第1の制御ループは、モーター軸の回転を検出し指令値通りのモーター回転速度で動作させるためのフィードバック制御ループである。この制御ループだけでは定着ローラーの熱膨張などによる周速度変化を抑制できないため、ロール紙走行速度に変動が発生してしまう。
第2の制御ループは、定着ローラーの1回転変動を精度良く抽出するためのローパスフィルター(LPF)と平均化処理で構成されている。
前述の通り、定着ローラーの周速度変動はロール紙の走行性に大きく影響しているため、定着ローラーの周速度変動を精度良く抽出し、第1の制御ループに適切な指令値を送る事が重要である。しかし、検知ローラーで検知したロール紙走行速度信号には他駆動で発生する高次の変動も含まれており、このままでは精度の高い制御を行うことが出来ない。
そこで、第2の制御ループでは、LPFを工夫して2段のカスケード接続とした。これによりカットオフ周波数を急峻にすることができ、且つ、変動成分を再現させる平均化処理を加えることで、制御対象である定着ローラーの周速度変動のみを精度よく抽出する事が可能となった。
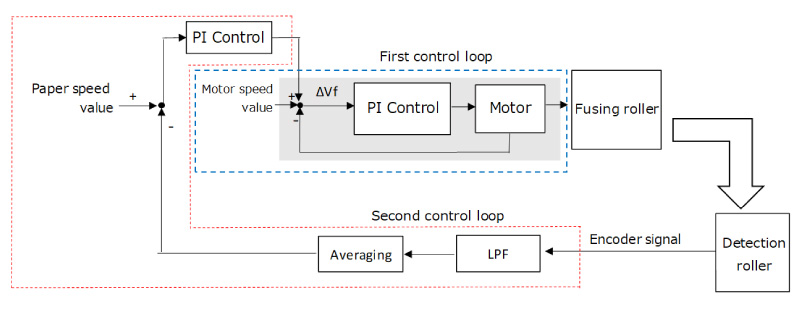
Fig. 4 Control block diagram.
5 リアルタイム色ずれ補正
リアルタイム色ずれ補正は大きく分けて2つのStepで構成される。ここではStepごとに説明する。
Step1.<色ずれ算出>:測定用パッチ画像のスキャン及びずれ量演算。
Step2.<色ずれ補正>:演算された色ずれ量に応じて、画像処理により色ずれを補正。
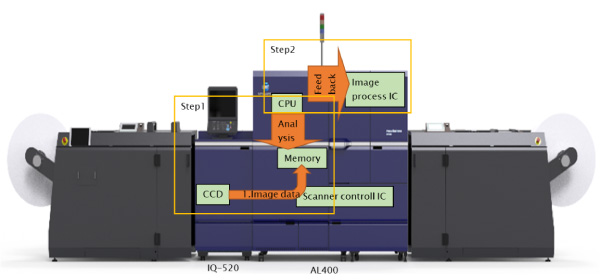
Fig. 5 Real-time color registration system configuration.
5.1 Step1色ずれ算出
本Stepでは、ロール紙端部へ色ずれ測定パッチを配置し、IQ-520内に設置されたインラインスキャナーでパッチをスキャンし演算装置(CPU)で画像解析を行うことで色ずれ量を算出する。
具体的には、Fig. 6 (a)に示すパッチをスキャンした画像Fig. 6 (b)から各パッチ重心座標を算出し、重心座標差とパッチ設計値との差異を色ずれ量とする。
ただし、AL400では連続して印刷するロール紙に対してスキャンを行うためスキャン中の用紙搬送速度は印刷速度と一致させる必要があり、画像解像度は200dpi程度となる。200dpi 1dotは127μmであり、画素単位で重心位置を算出すると127μm単位での色ずれしか算出できず目標とする色ずれ軽減を達成できない。
そこで、スキャン画像の各画素RGB値が100%未満の画素については、その画素の下部、または、上部だけにパッチが存在するとみなすことで重心位置の算出を行った(Fig. 7 (b))。例えば、Bkパッチ部のRGB平均値が30%なら0.3dotまでパッチが存在しているとみなして算出を行った。なお、CMYパッチはRGB成分の内、CMYとRGBで補色の関係にある成分を使用した(YならB成分)。
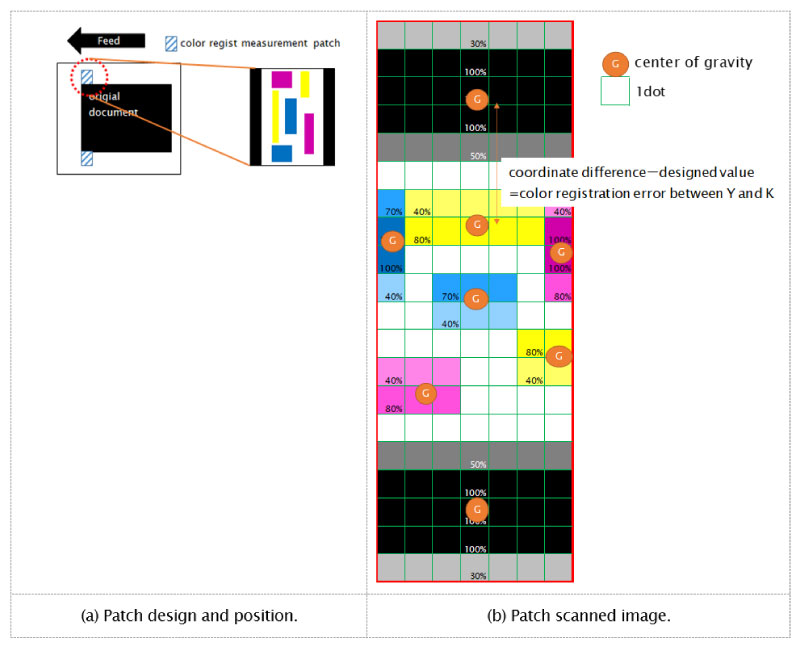
Fig. 6 Color registration measurement patch design.
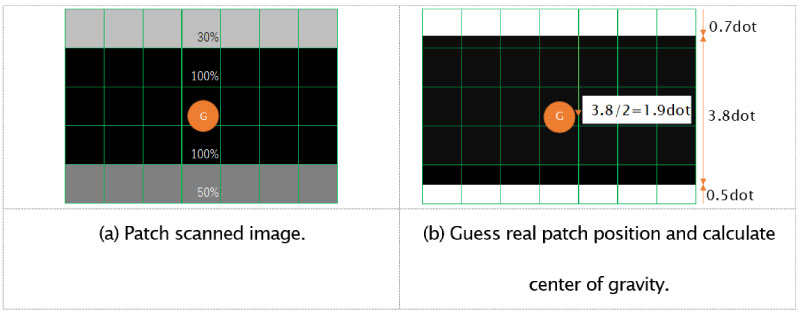
Fig. 7 Detail of calculate center of gravity.
5.2 Step2色ずれ補正
本Stepでは、Step1で算出された色ずれ量に基づいて、画像処理によってページ単位で色ごとに画像位置を動かすことで印刷中に色ずれを補正する。Table 1に示す2つの手段を組み合わせて補正を行う。
Table 1 Comparison of correction method.
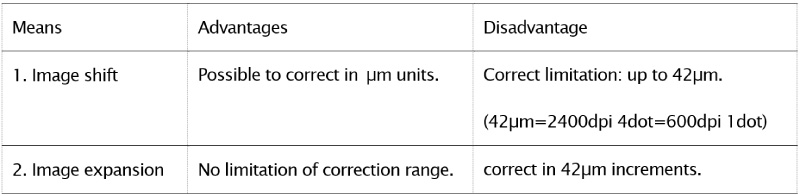
手段1は、画像データを平行移動させることで色ずれを補正する。ただし、AL400の解像度は主走査1200dpi×副走査2400dpiであり、単純なシフトでは2400dpi 1dotである10.6μm単位での補正しかできない。そこで、主走査数画素おきに1dotだけをシフトさせることで平均的に1dot未満のシフトとした。例えば、主走査8画素中1画素だけシフトした場合は10.6/8=1.3um相当のシフトとなる(Fig. 8)。
なお、本手段1では、原稿画像の欠損を防ぐためシフト後には画像先端に余白が発生することになる。よって、本手段のみを用いて全ての色ずれを補正するにはページ間に大きな隙間が必要になるため、後述の手段2を組み合わせることでページ間隙間を42μmに抑えた色ずれ補正を実現した。
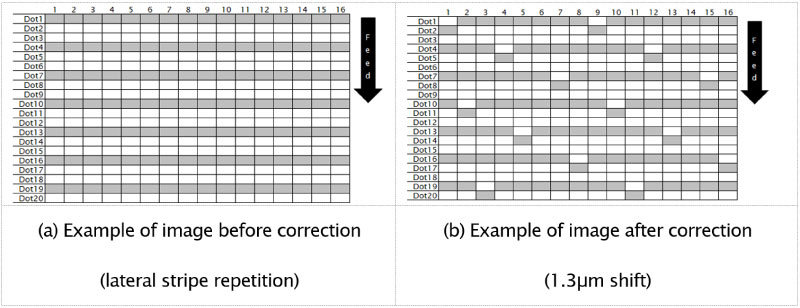
Fig. 8 Detail of method 1.
手段2は、画像データの後端へ余白画素を挿入する。AL400の副走査書き込み解像度は2400dpiだが内部では画像データを4dot単位で処理しているため、余白画素も4dot単位=600dpi 1dot単位での挿入となる。本手段ではFig. 9のように、色ごとに画像サイズを変えることで色ずれ補正を実現している。
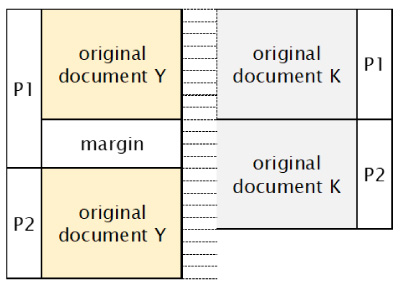
Fig. 9 Detail of method 2.
手段1と2を組み合わせた例をFig. 10に示す。この例ではP1からP2の間でYに2dot、P2からP3の間でさらに2dotの色ずれ補正を適用し、P3では合計4dotの補正となった。Table 1で示した通り手段1の補正は最大4dotまでとなるため、P3で手段2による余白4dot挿入を行う。こうすることで、手段1のシフト量は0に戻り再び4-8dotまでの微小な補正を実行できるようになる。
このように、手段1による補正と、手段2による補正、および、手段1の補正値リセットを繰り返すことでリアルタイム色ずれ補正を実現している。
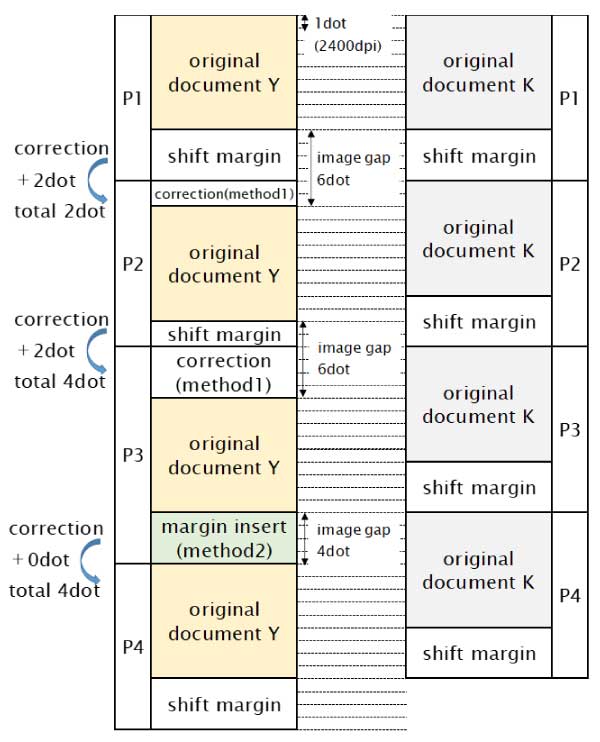
Fig. 10 Example of real-time color registration correction.
6 まとめ
2つの技術を採用することでロール紙特有の長周期の動的変動を抑制することができ、前任機AccurioLabel 230に対し色ずれに対する画像品質を25%改善することができた。また、生産性要求であるロール紙の連続走行距離も300mから3,000mまで伸ばすことが可能となった。
Fig. 11に用紙速度制御、リアルタイム色ずれ補正の採用前後の結果を示す。プリント初期からの色ずれの変化量を500m間隔でプロットしたものである。走行距離が延びるにつれて色ずれの変化量が60μm悪化していたものが、リアルタイム色ずれ補正の効果により20μmの色ずれの変化量に低減できた。
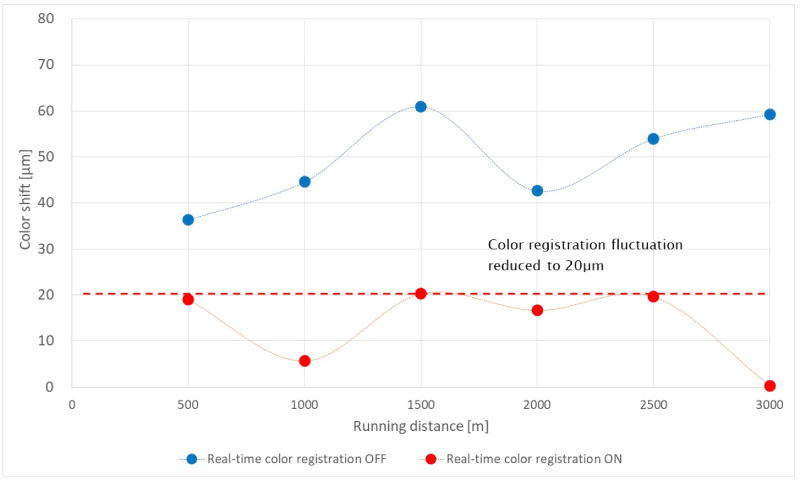
Fig. 11 Transition of color registration from the beginning of printing.
印刷業界における人財不足や、ビジネスモデルの変革により、デジタルカラー印刷機の適用範囲は広がり、その中でもラベル・パッケージ印刷市場はデザインと連携し、コンシューマー商品の満足度を上げる手段の一つとして拡大している。それゆえに、デジタルラベル・パッケージ印刷機はコンシューマー向けラベル生産機として位置づけられ、生産性や画像品質に対する要求はさらに高くなってくると予想される。
今後は、さらなるロール紙の走行メカニズム解明に基づいて最適な画像形成手段を適用し、お客様に高い画像品質を提供していく。